As technological advancements continue to shape the energy sector, well casing coupling remains an indispensable component ensuring the safety and efficiency of oil and gas extraction processes. With a robust focus on experience, expertise, authoritativeness, and trustworthiness, understanding the intricate role of well casing coupling is crucial in sustaining operational reliability and optimizing production performance.
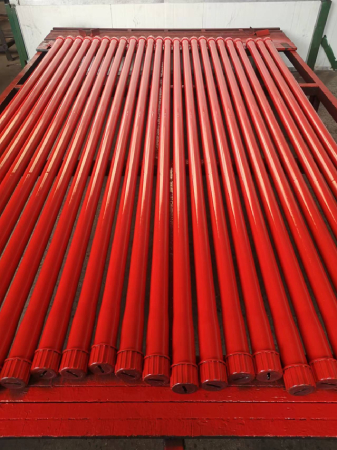
In the realm of subsurface drilling, well casing coupling serves as the pivotal link that joins segments of casing pipes, which line the borehole of an oil or gas well. These couplings not only safeguard the structural integrity of the well but also prevent unwanted fluid migration between the drilled layers, thus preserving the desired pressure levels within the reservoir. With well casing often subject to harsh environmental conditions deep underground, the choice and maintenance of high-quality coupling become vital.
From an experiential perspective, numerous drilling operations have demonstrated that choosing the right coupling materials significantly mitigates the risks associated with high-pressure and high-temperature environments. Premium couplings forged from alloy steel exhibit excellent resistance to thermal stress and corrosion, outperforming their counterparts in extreme conditions. Industry veterans advocate for the use of API-grade couplings, which adhere to stringent standards set by the American Petroleum Institute, ensuring that they meet the necessary durability requirements for varied subsurface conditions.
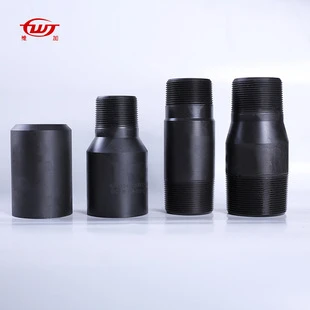
Expert analysis highlights that incorrect selection or installation of casing couplings can lead to catastrophic failures, including blowouts or casing leaks, which are not only hazardous but also financially burdensome. Ensuring that the engineering team is proficient in installing these couplings with precision is key to preventing such operational setbacks. Employing non-destructive testing methods, such as ultrasonic testing or magnetic particle inspection, is recommended to inspect the integrity of couplings during their lifecycle, thereby averting potential downtimes.
well casing coupling
Delving into authoritative guidelines, the deployment of well casing couplings is meticulously governed by industry standards, including those from the International Organization for Standardization (ISO). These directives offer a comprehensive framework for manufacturers and operators alike, detailing the requisite dimensions, threading types, and tensile strengths necessary to withstand operational pressures. By adhering to these channelized regulations, companies can ensure that they remain compliant with safety protocols while minimizing operational risks.
Trustworthiness in the realm of casing couplings comes from consistent quality assurance and maintaining a track record of reliability. Leading manufacturers undergo rigorous certification processes to verify that their products not only meet but exceed industry standards. Testimonials from seasoned engineers and operators further substantiate the reliability of these products and their critical role in the structural fortitude of wellbores.
Finally, embracing technological innovations in coupling designs, such as self-sealing or expandable couplings, has revolutionized well integrity management. These advancements provide added layers of leak prevention and adaptability, particularly in complex well architectures. Continuous investment in research and development by leading companies ensures that cutting-edge solutions are both practical and scalable, addressing the evolving demands of modern drilling operations.
In conclusion, well casing coupling, though a seemingly modest component, holds the key to achieving efficient, safe, and sustainable oil and gas extraction. Through a concerted emphasis on experienced selection, expert machinery handling, authoritative adherence to standards, and trustworthy manufacturing, the industry can harness the full potential of this essential technology. As the energy landscape continues to evolve, maintaining an unwavering focus on these four pillars will ensure that businesses remain at the forefront of operational excellence and innovation.