In the complex field of oil and gas extraction, well tubing and casing play a pivotal role in ensuring both safety and efficiency. Understanding the distinct functionalities and technical nuances of these two essential components not only supports better drilling practice but also significantly impacts the bottom line of oil production companies. In this exploration, we delve into the intricacies of well tubing and casing, emphasizing their critical differences and the implications of choosing the right specification.
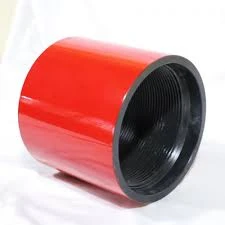
Well tubing and casing are indispensable components used during the drilling and operation of oil and gas wells. They might appear similar to the untrained eye, given that both are cylindrical pipes inserted into the drilled wellbore, but their functions, materials, and installation processes vastly differ.
Casing is the first to be introduced into the well bore. Its primary function is to stabilize and reinforce the well walls, preventing unwanted substances from entering the well stream. Moreover, it acts as a protective barrier, isolating high-pressure zones. Casing is crucial in preventing blowouts—a catastrophic event where uncontrolled fluid release occurs due to pressure imbalances. Selecting the right casing involves considering factors such as pressure tolerance, corrosion resistance, and the harshness of the subterranean conditions it will face. Special types of casing, like conductor casing and surface casing, serve specific depths and functions. Installations often require cementing the casing to the well bore, ensuring a firm and impermeable bond. This step lays down the foundation for subsequent operations on a solid and reliable base.
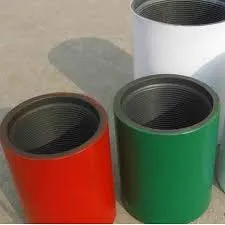
Tubing, introduced after casing, serves a different yet equally important role. It is the conduit for transporting oil and gas from the bottom of the well to the surface. Unlike casing, tubing is not cemented, allowing it to be more flexible and manageable for maintenance and replacement. The tubing string is subjected to dynamic stresses from fluid pressures and temperatures, necessitating meticulous material selection such as high-strength steel alloys and, in some cases, corrosion-resistant materials. Tubing ensures that produced fluids are safely and efficiently brought to the surface for processing, with several tubing strings sometimes being utilized in deeper wells to maintain optimum production rates and flow integrity.
The marriage of precision engineering and material science plays a critical part in the development of both casing and tubing, where industry standards like API (American Petroleum Institute) specifications provide rigorous benchmarks to ensure operational safety and efficiency. These specifications guide manufacturers in producing components that can withstand extreme subterranean environments, whether battling the corrosive effects of carbon dioxide and hydrogen sulfide or enduring high-pressure and high-temperature conditions in deep wells.
well tubing and casing
Expertise in well tubing and casing selection and installation is vital not only for maintaining operational safety but also for optimizing the lifespan and productivity of wells. Incorrect sizing or material choice can lead to catastrophic failures such as tubing rupture or casing collapse, resulting in halted production and massive financial losses. Therefore, oil and gas operators must engage with seasoned petroleum engineers and geologists who provide authoritative assessments based on data-driven simulations and field experience.
Trustworthiness in this domain is further bolstered by collaborations with respected manufacturers known for their stringent quality control processes and innovation in metallurgy and pipe technology. Companies prioritizing sustainability are also gaining traction, producing environmentally considerate alternatives, such as premium connections that minimize leakage risks and eco-friendly well-servicing protocols.
The future of well tubing and casing leans heavily on innovations like smart casing sensors and real-time monitoring systems, which enhance traditional practices by providing instant data feedback, allowing operators to make informed decisions swiftly. This technological leap, paired with the ongoing development of composite materials, promises a path toward even more reliable and efficient oil and gas operations.
In conclusion, well tubing and casing are fundamental to the safe and efficient extraction of oil and gas. Expertise in understanding their roles, selecting appropriate materials, and leveraging advanced technologies defines the success of extraction operations. Companies must remain at the forefront of these technological advancements and maintain a commitment to authoritative and trustworthy practices to meet today's industry demands. Through strategic selection and innovative engineering, oil and gas operations can ensure robust well integrity, extend the life of production sites, and achieve greater operational efficiency.