In the realm of oil and gas drilling, understanding the distinctions between casing and tubing is crucial for optimizing well performance and ensuring operational safety. Both play pivotal roles in the extraction process, but their functions, specifications, and applications vary significantly.
This article delves into the core differences between casing and tubing, offering insights grounded in industry expertise and firsthand operational experience.
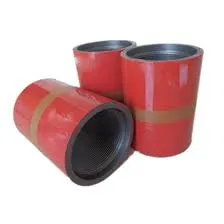
Casing is essentially the backbone of a wellbore, providing structural integrity and stabilizing the well during drilling and production. It is a large diameter pipe installed in sections, which are cemented in place in the drilled hole. The primary purpose of casing is to prevent the wellbore from collapsing under external geological pressures and to isolate different underground layers, protecting freshwater aquifers from contamination and preserving the integrity of oil and gas zones.
On the other hand, tubing is much smaller in diameter compared to casing and is not cemented. Its primary function is to transport produced fluids—oil, gas, or water—from the wellbore to the surface. Tubing is designed to withstand high-pressure flows and to protect the inner walls from corrosive substances. Its removable and replaceable nature facilitates routine maintenance and optimization without compromising the well’s structure.
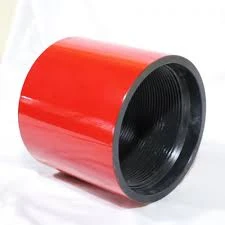
A significant exploration in distinguishing these two components lies in their design standard and material composition. Casing is typically made from steel alloys designed to endure high external pressure and axial stress, ensuring long-term durability. Specifications often adhere to standards such as API 5CT, which dictates strength categories and testing protocols to certify the casing’s ability to handle subterranean conditions.
Conversely, tubing is crafted with an emphasis on flexibility and strength to handle the dynamic internal pressures from hydrocarbons and injected fluids during operations. Tubing must withstand not only the chemical compositions of fluids but also varying pressure differentials as environmental conditions change. Standards such as API 5L are frequently referenced for specifying material and fabrication processes that ensure the robustness of tubing in demanding operational contexts.
what are the differences between casing and tubing?
Operational deployment of casing and tubing also exhibits distinctive methodologies. Casing is run and cemented during various phases of drilling, classified into surface casing, intermediate casing, production casing, and sometimes additional conductor casing based on well depth and environmental conditions. Each layer is tailored to the stage of drilling, intended to incrementally protect and progressively deepen access to the reservoir.
Tubing, introduced during the completion stage, is paramount for the production phase. It connects directly to the surface collection systems. Operators often utilize advanced completion techniques, including multiple tubing strings or utilizing corrosion-resistant alloys, to maximize recovery and prolong the operational lifespan of the well.
The choice between different types of casing or tubing depends on site-specific requirements and economic considerations. Longevity, regulatory compliance, and environmental protection are at the forefront of these decisions, making the selection process critical to minimizing risk and optimizing resource extraction.
In summary, understanding the distinction between casing and tubing involves recognizing their specific roles, the engineering standards they must meet, and their deployment strategies. Casing provides structural support and environmental safeguarding, while tubing serves the production phase's operational needs. For industry professionals, this knowledge is not only foundational but vital to ensure efficient, safe, and successful hydrocarbon recovery operations.