In the world of oil and gas extraction, understanding the difference between casing and tubing is fundamental for both engineers and those involved in the production process. These two components serve distinct purposes, undergo different stress conditions, and have unique design requirements, making their distinction crucial for operational success and safety in drilling operations. This article delves into each component's role, providing insights backed by expert knowledge and industry experience.
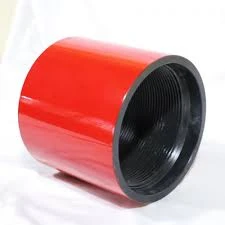
Casing and tubing are integral parts of well construction in the oil and gas sector, but each serves a unique function within the wellbore. Casing is a large-diameter pipe assembled and inserted into a recently drilled section of a borehole, whereas tubing is a smaller-diameter pipe inserted inside the casing string, through which oil and gas are produced.
Starting with casing, its primary purpose is to stabilize the drilled hole, isolate different underground formations, and prevent the hole from caving in. The casing also protects fresh water zones from contamination by drilling fluids or hydrocarbons. Typically, the casing process involves running multiple strings—each getting progressively smaller in diameter and longer in length—and installing and cementing them in place to create layers of protection and isolation. The technical expertise involved in selecting and installing casing depends on understanding geological conditions and pressure regimes, which can vary significantly across fields. Experienced engineers utilize specialized software and strict regulatory standards to design casing strings that withstand downhole pressures, temperatures, and chemical exposure.
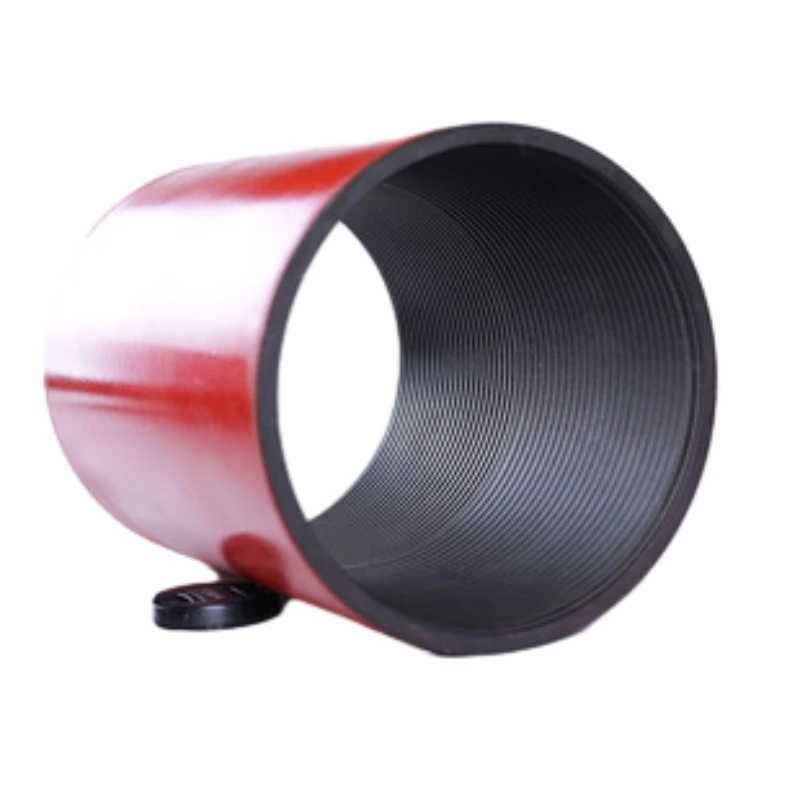
Tubing, on the other hand, is primarily associated with production. Once the well has been drilled and cased, tubing is run into the wellbore, through which oil and gas flow to the surface. Unlike casing, which is cemented in place, tubing is removable and can be replaced over the lifetime of the well. Its design considerations focus more on internal pressure containment and pressure drop efficiency since it directly conveys hydrocarbons. Materials used need to withstand high pressures, corrosive fluids, and extreme temperatures. Expertise in tubing includes knowledge of various types, such as coiled, jointed, or continuous tubing, depending on the well's requirements.
what are the differences between casing and tubing?
The authoritative and trustworthy selection of casing and tubing relies heavily on real experience and stringent adherence to industry standards. Casing design demands a sound understanding of the mechanical properties of steel, cementing practices, and formation pressures, validated through years of field learning and lessons from documented case studies. Trustworthiness in the industry emerges from accurate simulations, reliable testing, robust supply chain management, and alignment with international standards like API (American Petroleum Institute) specifications.
Moreover,
the differences between casing and tubing extend to the maintenance and inspection requirements. Casing integrity is usually verified via logging tools that assess cement bond quality and detect any potential breaches, using instruments such as caliper logs or casing inspection logs. Tubing inspection involves regular checks to prevent leaks, scale build-up, and corrosion. Technologies like electromagnetic inspection, ultrasonic testing, and pressure testing help ensure the tubing's integrity, contributing to a well's safe and efficient operation.
Innovations are continually emerging in both casing and tubing designs. Enhanced materials, such as corrosion-resistant alloys and high-strength steels, are becoming more prevalent to address harsher downhole conditions and extend the service life of wells. Smart well technologies involving sensors integrated into casings and tubing help monitor real-time downhole conditions, offering improved diagnostics and operational efficiencies.
Understanding the pragmatic differences between casing and tubing is pivotal in well architecture and operational decision-making. While both serve to optimize oil and gas extraction, careful consideration of their unique properties and functions, backed by experience, expertise, authority, and trust, drives successful and sustainable well operations. To thrive in this arena, industry professionals must continually advance their knowledge and practices in designing and maintaining these critical components.