When delving into the intricacies of the oil and gas industry, understanding the distinction between casing and tubing is crucial for both industry professionals and investors alike. These two components, while often confused, play vitally different roles in the extraction and production process of hydrocarbons.
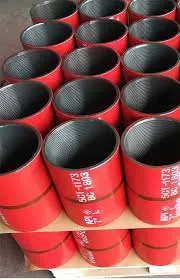
Casing, in its simplest form, refers to the heavy-duty pipe inserted into a newly drilled wellbore. It serves multiple essential functions isolation of different underground strata, reinforcement of the wellbore structure to prevent collapse, and safeguarding against contamination of groundwater with drilling fluids or hydrocarbons. Casings are typically made of steel and come in various diameters and grades depending on the depth and pressure requirements of the well. The installation of casing is a complex process that requires precise engineering expertise to ensure the structural integrity of the well, thereby emphasizing the need for experienced personnel to oversee operations.
On the other hand, tubing is a smaller-diameter pipe placed inside the casing. Its primary function is to transport oil and gas from the reservoir to the surface.
Tubing must withstand different pressures and temperatures compared to casing as it directly interacts with the extracted fluids. Unlike casing, which is cemented in place, tubing can be replaced or removed as needed. This aspect of tubing highlights the importance of operational flexibility in managing reservoir production rates and maintenance schedules. Tubing strings are subject to wear and tear due to continuous exposure to the corrosive nature of extracted hydrocarbons and require regular monitoring to ensure performance consistency—a fact that underscores the expertise needed in inspection and maintenance protocols.
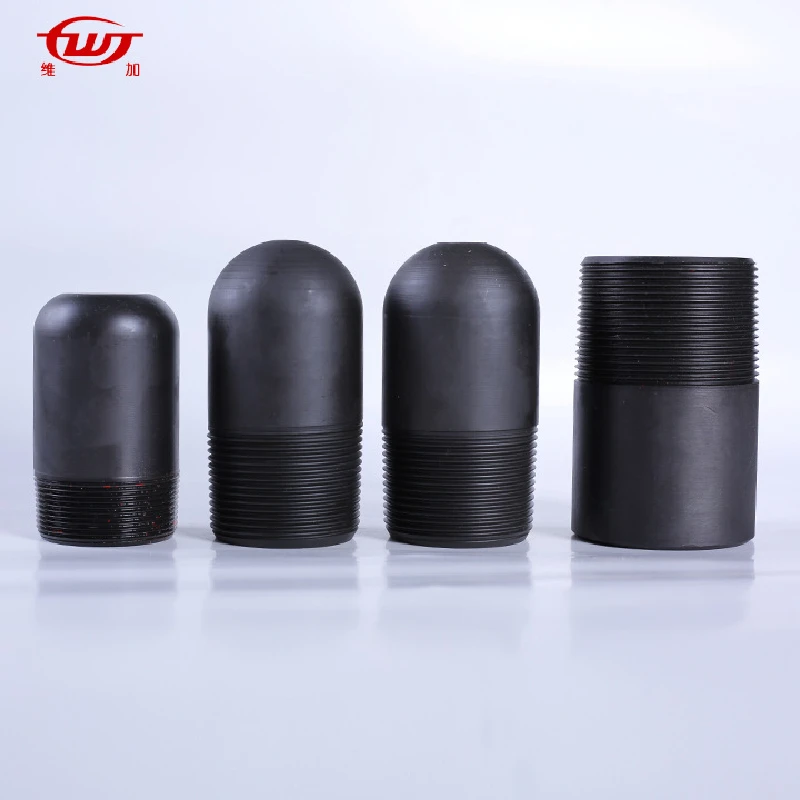
The expertise required in making decisions about casing and tubing extends beyond the materials and installation practices. The selection of suitable casing and tubing involves a thorough understanding of geophysical data, reservoir characteristics, and economic factors. An authoritative figure in the industry would highlight that technological advancements have revolutionized materials science, allowing for the development of more durable and corrosion-resistant alloys used in both casing and tubing. Innovations such as these represent a pivotal shift towards enhancing the lifespan and efficiency of well components, improving the overall trustworthiness of well operations.
what are the differences between casing and tubing?
Through real-world experience, industry experts have learned that improper selection, installation, or maintenance of casing and tubing can lead to catastrophic failures such as blowouts or environmental contamination. Such potential risks emphasize the importance of a coherent understanding of well mechanics and the establishment of stringent safety protocols. Regulatory bodies often impose strict compliance measures to ensure that oil and gas operations undertaken by companies prioritize environmental safeguarding and worker safety. Trustworthiness in this industry is built upon adherence to these standards as well as demonstrated proficiency in risk management strategies.
Therefore, while casing and tubing are fundamentally different in function—casing serving as structural support and tubing as a conduit for extracted resources—their synergistic role is indispensable in the success of any drilling operation. Insights provided by seasoned professionals underscore that the selection process is as much about understanding the subsurface environment as it is about engineering precision. Industry leaders entrusted with these responsibilities focus on leveraging technological advancements and data analytics to drive innovation and enhance operational efficiency. This not only maximizes resource extraction but also fortifies the industry's commitment to environmental stewardship and safety, creating a trajectory of continual improvement and sustainability.
In conclusion, comprehending the divergences between casing and tubing is not merely a matter of distinguishing between two sets of pipes; it is about recognizing their collective contribution towards achieving industry goals safely and efficiently. Expertise and authoritative decision-making are key to navigating the complexities inherent in using these components effectively, and trust in these processes assures stakeholders of their value and efficacy in the ever-evolving landscape of oil and gas exploration and production.