In the oil and gas industry, the terms casing and tubing are fundamental yet often confused components within drilling operations.
Understanding the key differences between the two is crucial for anyone looking to gain a deeper insight into this energy sector.

Casing and tubing both serve as integral parts of the drilling process, but they are employed at different stages and serve distinct purposes. Let's dive into what sets these two apart.
Casing is the initial layer of pipe that is installed into a drilled hole. Its main function is to stabilize the well and prevent the borehole from collapsing. Casing also protects the well by isolating the different layers of soil and fluids encountered during the drilling process. By sealing off these layers, casing helps in preventing contamination of fresh water zones and mitigates risk factors such as blowouts, which can occur when a pressurized pocket of gas or oil is unintentionally intersected. This makes casing a crucial safety component in drilling operations.
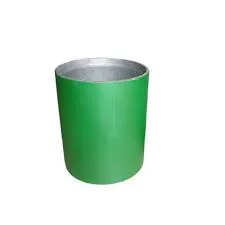
Varieties of casing include conductor casing, surface casing, intermediate casing, and production casing, each serving specific roles in terms of depth, pressure requirements, and geological conditions encountered. For example, surface casing is extended to prevent contamination of water, while production casing is set through productive oil or gas zones to facilitate efficient extraction.
Tubing, on the other hand, is installed inside the production casing and its primary role is to transport the oil and gas from the reservoir to the surface. Unlike casing, which remains static, tubing often needs to be replaced or adjusted during the life of the well as it is subject to wear and tear from the continuous flow of hydrocarbons. Tubing is thus designed to withstand the pressures and corrosive nature of the extracted fluids.
The differentiating factor between casing and tubing is not just their form or function, but also the materials used and the operational techniques applied. Tubing often uses high-grade alloys to resist corrosion and pressure, while casing may vary in terms of material strength depending on the depth and environmental conditions it needs to withstand.
what are the differences between casing and tubing?
The installation of casing and tubing is an engineering endeavor supported by extensive geological research and predictive modeling. Much of this expertise is derived from experimental data and field studies that demystify subsurface conditions. Industry professionals rely on this data to make informed decisions, balancing efficiency and safety.
Often, casing has larger diameters compared to tubing, reflecting its function in providing structural integrity, while tubing is designed for flow efficiency. However, the challenge lies in choosing the correct specifications, as errors could lead to operational setbacks or catastrophic failures. Consequently, project managers and engineers prioritize high-quality materials and precise engineering, often working closely with manufacturers who specialize in producing oilfield components meeting industry standards.
Advancements in technology have continuously improved the design and application of casing and tubing, introducing innovations like smart tubing equipped with sensors for real-time data collection. These developments further enhance the efficiency, safety, and economic viability of drilling operations.
From both an experiential and expert perspective, the mastery of application and understanding of both casing and tubing are indispensable for optimizing oil and gas extraction. Decision-makers must weigh geological insights against financial and environmental considerations, ensuring that their implementations are guided by the latest industry practices and technological advancements.
Highly experienced oilfield professionals and engineers oversee the planning and implementation phases, leveraging their authoritative knowledge to maximize resource extraction while minimizing environmental impact. Trustworthiness in handling such critical operations is validated by industry certifications and adherence to international safety protocols, ensuring operations are conducted responsibly and sustainably.
In conclusion, while casing and tubing are often mentioned in tandem, their differences in function, application, materials, and design underscore their individual significance within the complex process of oil and gas extraction. Understanding these differences enhances operational effectiveness and safety, confirming their indispensable roles in the petroleum industry.