Understanding the bull plug, often encountered across various industries such as oil and gas, is essential for professionals striving for operational excellence. A bull plug is a crucial component engineered to serve specific purposes within a pipeline system or as part of a pressure containment mechanism. Its unique design, typically featuring a solid, cylindrical shape with threading on one or both ends, allows it to seal off a section of the pipeline effectively.
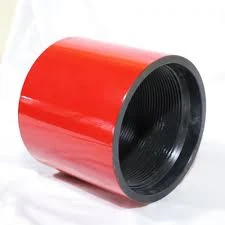
Many experts recognize the bull plug's importance in scenarios requiring the temporary or permanent closure of piping systems. For example, during maintenance or testing, the bull plug acts as a cost-effective and robust solution to contain pressure and prevent unwanted fluid flow, ensuring the safety and efficiency of operations. It is engineered to withstand various pressure conditions, making it indispensable in high-stakes environments such as deep-sea oil rigs.
From an engineering perspective, the selection and application of a bull plug involve considerable expertise. Professionals must consider factors such as material compatibility, pressure ratings, and size specifications to align with system requirements. Common materials used include stainless steel, brass, and carbon steel, each chosen for its resistance to corrosion, durability, and pressure-bearing capacity. Thus, a bull plug must not only adhere to strict industry standards but also undergo rigorous testing to verify its reliability under extreme conditions.

The authority and trustworthiness of information surrounding bull plugs are often supported by detailed industry standards and certifications. Organizations like the American Petroleum Institute (API) and the American Society of Mechanical Engineers (ASME) provide guidelines ensuring that bull plugs meet safety and performance criteria. Compliance with these standards is not only a testament to a manufacturer's commitment to quality but also a legal requirement in many regulatory environments.
what is a bull plug
For industry professionals sharing their experiences, the real-world application of bull plugs often highlights their versatility and indispensable nature. Whether used in plumbing, chemical processing, or oil extraction, firsthand accounts often reveal how bull plugs solve specific challenges. These narratives underscore the component’s efficacy in preventing system failures and ensuring smooth operational workflows.
In practice,
successful usage of bull plugs is a testament to the expertise of engineers and operators. A well-chosen and installed bull plug prevents leaks and manages pressure, ultimately safeguarding personnel and equipment. Moreover, it reflects a well-rounded understanding of the system’s intricacies, reinforcing the idea that experience is as valuable as theoretical knowledge in field operations.
In summary, the bull plug stands out as a vital product within its industry, seamlessly integrating expertise and trustworthiness in its function. By adhering to rigorous standards and leveraging professional expertise, the bull plug continues to be a reliable solution for sealing and pressure management across diverse applications. As industries evolve, the bull plug remains a steadfast component, exemplifying engineering excellence and operational reliability.