The term bull plug might not be widely recognized by those outside of specific technical or industrial fields, yet it plays a significant role in various applications, notably in the oil and gas industry. Its importance stems from its utility in maintaining safety and efficiency within drilling operations. This article delves into the detail surrounding bull plugs, exploring their design characteristics, usage, industry applications, and safety considerations.
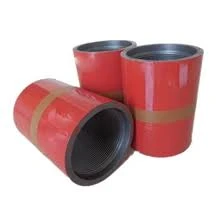
A bull plug, fundamentally, is a solid plug used at the end of a piping system or in a pipeline. Its primary function is to permanently or temporarily seal the end of a pipe, preventing the flow of fluids. Typically manufactured from high-quality materials, such as carbon steel, stainless steel, or other alloys, bull plugs are designed to withstand high pressure and corrosive environments. Their reliability in sealing pipeline systems makes them crucial components.
Experience in field operations underscores the vital role of bull plugs within the oil and gas sectors. In drilling operations, bull plugs are integral to maintaining control over the various fluids transported through the pipeline systems. During maintenance or emergency shutdowns, these plugs ensure that hazardous materials are securely contained, thus protecting workers and preventing environmental contamination. Some installations have reported that the failure to correctly implement bull plugs led to costly downtimes and repair operations.
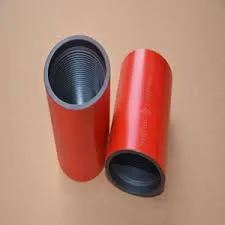
Expert knowledge is required to select the right bull plug for a specific application. Various factors must be considered, including pressure ratings, material compatibility, and environmental conditions. For instance, carbon steel bull plugs are preferable in environments where they are not subjected to extreme temperatures or corrosive substances. Conversely, stainless steel bull plugs are advantageous in harsher conditions due to their resistance to corrosion.
what is a bull plug
Authoritativeness is evident in industry guidelines and standards governing the manufacture and use of bull plugs. Organizations such as the American Petroleum Institute (API) and the American Society of Mechanical Engineers (ASME) provide comprehensive specifications that manufacturers and end-users must adhere to. These standards ensure that bull plugs are capable of withstanding the harsh conditions they may encounter, such as high-pressure environments typical of deep-sea drilling operations.
Trustworthiness in the industry comes from adhering to established protocols and leveraging products from reputable manufacturers known for their quality and compliance with international safety standards. For companies operating within high-risk industries, partnering with a reputable supplier of bull plugs is not just about ensuring operational efficiency but also about safeguarding their workforce and mitigating environmental risks.
Industries outside of oil and gas are beginning to acknowledge the importance of using proper sealing mechanisms like bull plugs. Industries dealing with chemical processing, water treatment, and even construction are deploying similar technologies for pipeline sealing due to the proven reliability of bull plugs. As the broader industrial landscape evolves with an increasing focus on safety and sustainability, the adoption of bull plugs is expected to expand.
In conclusion, bull plugs, though seemingly simple, are critical components in industries reliant on complex piping systems. Their ability to effectively seal pipelines and control fluid transport underscores their importance. Understanding their application, material selection, and adherence to industry standards can significantly enhance operational safety and efficiency. As sectors continue to evolve and prioritize environmental sustainability, the demand for high-quality bull plugs is anticipated to grow, reaffirming their essential role in industrial operations.