Understanding the intricacies of equipment and components in various industries is crucial for optimal performance and safety. A term that often arises in industrial, mechanical, and oil field discussions is bull plug. Despite its seemingly simple nature, a bull plug plays a significant role in various applications.
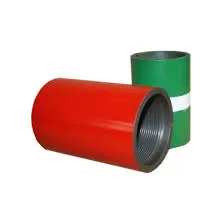
The bull plug is a vital component primarily used in pipelines and oil field operations. It is essentially a solid metal fitting, typically cylindrical, designed to terminate pipe sections. When a pipeline or system requires temporary or permanent sealing, the bull plug comes into play, blocking the flow of fluids or gases efficiently. They are commonly crafted from robust materials such as stainless steel or carbon steel to withstand high pressure and varying environmental conditions.
From a practical standpoint, bull plugs are invaluable in maintenance and modification scenarios. Suppose a pipeline needs servicing or an additional component's installation; a bull plug can be used to temporarily seal the line during the procedure, ensuring safety and preventing fluid loss. For professionals in the oil and gas industry, understanding the correct application and specifications of a bull plug is essential for maintaining system integrity and safety standards.

Bull plugs come in various sizes, adhering to standard pipe dimensions, ensuring compatibility across systems. The dimensions range from small-scale plugs used in minor applications to large plugs required for industrial pipelines. The choice of size and material depends on the specific requirements of the pipeline, such as pressure tolerance and environmental exposure.
The expertise in selecting and utilizing bull plugs cannot be overstated. Engineers and pipeline operators rely on technical manuals, industry standards like API (American Petroleum Institute) norms, and practical experience to guide their choices. Incorrect use or a mismatch in specifications could lead to leaks, system failures, or catastrophic safety incidents, underpinning the bull plug's critical role in operation protocols.
what is a bull plug
Trustworthiness and reliability in bull plug manufacturing are essential. Reputable manufacturers will provide full material certifications, pressure testing data, and compliance documentation to establish their products as safe and effective. Ensuring that the bull plugs have undergone rigorous quality control processes provides the necessary reassurance to engineers and safety inspectors.
Authoritativeness in the context of bull plugs involves continuous research and adaptation to industry changes. Manufacturers are frequently developing new materials and designs to enhance durability and efficiency under diverse conditions. Keeping abreast with these innovations not only improves operational efficiency but also aligns with sustainability and regulatory standards that industries are increasingly focusing on.
Real-world experiences underscore the importance of bull plugs. In countless cases within the oil and gas sector, their use has prevented potential disasters by allowing safe and effective pipeline shutdowns during maintenance or emergencies. This highlights the vital role that knowledge and proficiency in the use of such components play in broader operational procedures.
In summary, while bull plugs may appear to be just another component within the vast array of industrial equipment, their impact is far-reaching. They are a cornerstone in pipeline safety and efficiency, and their proper selection and application are critical. Expertise in their use reflects a broader understanding of pipeline management, while trust in their manufacturing speaks to the integrity of operations. Adopting best practices in the use of bull plugs marks a commitment to excellence and safety in the face of evolving industrial demands.