A bull plug, a straightforward yet invaluable device, finds its quintessential applications within the oil and gas industry. This tool, often overlooked by those outside the trade, is essential for maintaining operational integrity and safety in drilling operations. Distinguished by its unique ability to ensure fluid control and pressure management, a bull plug stands as a silent guardian at the end of piping systems or tubing strings.
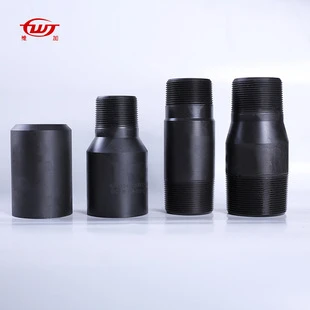
In the realm of industrial health and safety, the selection of appropriate equipment takes precedence, particularly when dealing with high-pressure systems. A bull plug, crafted typically from robust materials like stainless steel, carbon steel, or special alloys, ensures durability and resistance under extreme conditions. When evaluating its use, key considerations include the pressure rating, size, and the environment it will be deployed in, ensuring seamless integration into the existing system.
The primary function of a bull plug is to cap off or seal the end of a pipe. This seemingly simple task plays a critical role in various scenarios. It prevents any liquid or gas from escaping the system, facilitating the handling of unexpected surges in pressure effectively. Such functionality also maintains the cleanliness of the system by preventing contaminants from entering when the pipe is not in active use.
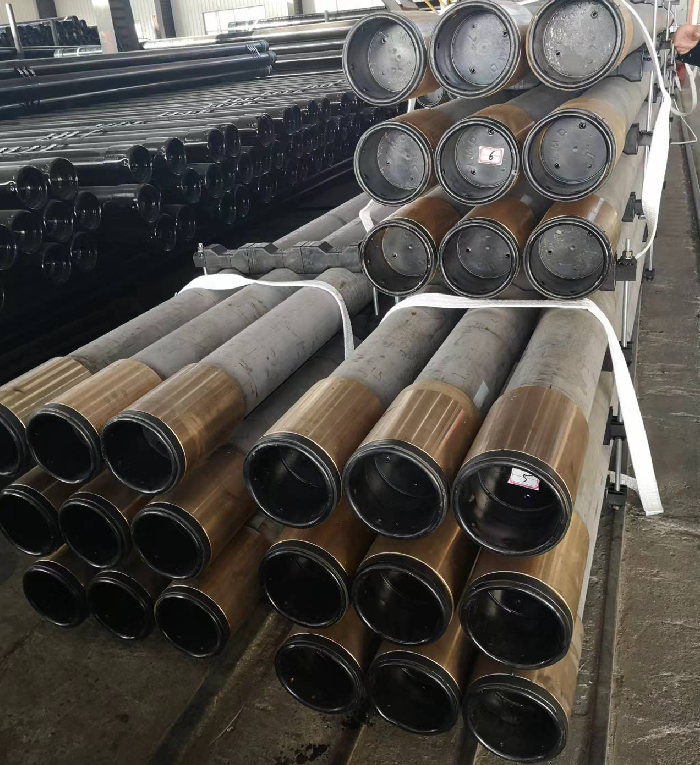
In practice, the use of bull plugs extends to applications beyond simple sealing. During maintenance, they allow sections of piping to be isolated without the need to drain the entire system. This is particularly useful during inspections, repairs, or modifications, facilitating optimal operational efficiency and reducing downtime. In projects where temporary termination of pipelines is necessary, bull plugs provide a cost-effective and reliable solution.
The oil and gas sector stands to benefit immensely from the reliability offered by bull plugs. In drilling processes, their role in controlling wellbore pressure cannot be overstated. By sealing ends of tubulars, they ensure that each stage of drilling can proceed safely and without unintentional fluid discharge or contamination. This aspect of operational integrity is pivotal when dealing with the inherently risky nature of extracting fossil fuels.
what is a bull plug used for
The expertise required to handle bull plug installations revolves around precision. Misaligned or improperly sealed bull plugs could result in leaks, leading to potentially hazardous situations. Thus, trained professionals ensure that fittings match the exact specifications required by the system, leveraging their expertise to prevent system failures.
Authoritative insight into the design and manufacturing of bull plugs reveals the meticulous engineering behind them. Compliance with standards such as the American Petroleum Institute (API) specifications assures users of their reliability and quality. Manufacturers invest significantly in testing these components under simulated conditions that mimic real-world pressures, ensuring that each bull plug can withstand the expected stresses of its intended applications.
Trust in the use of bull plugs is built through a history of consistent performance and safety assurance. Case studies from the field consistently demonstrate the efficacy of bull plugs in avoiding environmental spills and accidents. Since their introduction, these unsung heroes of the petrochemical world have become indispensable components of safety protocols, underpinning modern industrial practices with integral support for fluid management.
To sum up, bull plugs may be small, but their impact on operational safety and efficiency is monumental. Their integration into piping systems across the oil and gas industry illustrates a commitment to quality and reliability, withstanding the test of time and technological advances alike. As the industry continues to evolve, the reliance on trusted components like bull plugs remains a constant, ensuring uninterrupted and safe operations worldwide.