In the world of oil and gas drilling, every component plays a critical role in ensuring efficiency, safety, and productivity. Among these components is the pup joint, a less talked-about yet indispensable tool. Understanding what a pup joint is and its significance in drilling operations can offer great insights for industry professionals and enthusiasts alike.
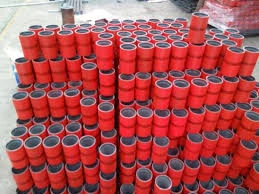
A pup joint is essentially a short piece of tubing used in the oil and gas industry. It comes in various lengths and is used to adjust the length of the drill string or casing string to accommodate specific well designs. The ability to precisely adjust the string length is crucial in reaching the desired depth and maintaining the integrity of the drill operation. Pup joints are predominantly used in two main scenarios when the standard lengths of drill pipe are insufficient to reach target depths and when fine adjustments are required to achieve perfect alignment with top drive systems or bypass tools.
The construction of a pup joint is as robust as the industry demands. They are manufactured from the same materials as standard drill rods or casings, often employing high-strength steel to withstand the extreme conditions found in drilling environments. This includes resistance to pressure, temperature, and corrosive substances. The ends of pup joints are threaded, allowing them to be easily connected to other components of the drill string with precision, minimizing the risk of leaks or structural failures.
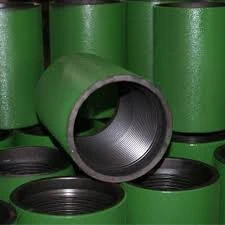
One of the most commendable aspects of pup joints is their versatility. They are not restricted to a single diameter or length, enabling them to be tailored to specific drilling needs. This adaptability extends to their role in customizing the bottom hole assembly (BHA). For instance, when integrating specialized tools that have specific operational lengths, pup joints can be used to adjust the overall assembly to ensure smooth operation and alignment.
what is a pup joint
From an economic standpoint, pup joints contribute significantly to cost-efficiency in drilling operations. The ability to make precise adjustments without having to replace entire sections of piping reduces material costs and minimizes downtime. This efficiency is crucial in an industry where every minute of rig time translates to substantial financial implications.
The expertise required to handle pup joints should not be underestimated. Handling and selecting the right pup joint involves understanding the well design, the materials’ specifications, and the environmental conditions of the drilling site. Moreover, it demands a thorough knowledge of the drill string dynamics and the ability to anticipate changes in downhole conditions. Operators and engineers need to work collaboratively to ensure that the right pup joint is selected, installed, and maintained throughout the drilling process.
Trustworthiness and authority in the use of pup joints are established through adherence to industry standards and regulations, such as those set by the American Petroleum Institute (API). Compliance ensures that the pup joints are manufactured and tested to withstand the operational demands and that they contribute to the overall safety and efficiency of drilling operations. This compliance is an assurance to stakeholders that the equipment used will not fail under pressure.
In conclusion, the pup joint, though small in comparison to other drilling components, is a cornerstone in optimizing drilling operations. Its applications are diverse and its impact on operational efficiency, cost reduction, and strategic flexibility cannot be overstated. Understanding and correctly utilizing pup joints involve a blend of experience, expertise, and adherence to industry standards. For companies striving to excel in the competitive landscape of oil and gas, mastery over every component, including the pup joint, is crucial. As the industry evolves, so too will the technology and application of these vital components, ensuring they remain a key piece in the drilling puzzle.