In the oil and gas industry,
understanding the distinction between casing and tubing is crucial for efficient and safe drilling operations. Both are essential components in the extraction process, yet they serve distinctive purposes and possess unique properties. Their appropriate application not only optimizes the efficiency of operations but also ensures the safety and integrity of the well. Let's delve into the specifics of how casing and tubing differ, and the roles they play in drilling operations, thereby emphasizing their importance.
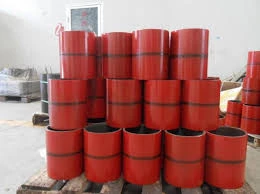
Casing refers to large diameter steel pipes that are used to line the drill hole, providing structural integrity to the newly drilled wellbore. This structural lining prevents the formation walls from caving in and protects the well stream from external elements such as water and other contaminants found in surrounding formations. It is installed in stages during the drilling process and is cemented in place to ensure stability and isolation of the wellbore from undesirable geological layers. Casing acts as a safeguard against potential hazards, including blowouts, and plays a critical role in maintaining control over the pressure during drilling operations.
In contrast, tubing is placed inside the casing and is a conduit through which oil and gas are transported from the wellbore to the surface facilities for processing and distribution. Tubing is smaller in diameter compared to casing and is designed to withstand the pressure and temperature changes involved in the extraction process. Unlike casing, tubing is not cemented in place; instead, it is hung from the wellhead and can be removed and replaced as necessary. This flexibility in design allows for ease of maintenance and replacement, which is vital in the lifespan of a well as production rates fluctuate and technologies evolve.
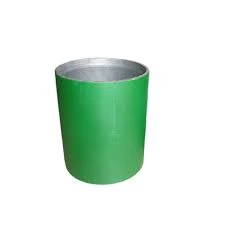
what is the difference between casing and tubing?
From an operational perspective, the choice between different grades and specifications of casing and tubing depends on several factors including the wellbore environment, the type of hydrocarbon being extracted, and economic considerations. For instance, sour gas wells, which contain hydrogen sulfide, require casing and tubing made of corrosion-resistant alloys. Understanding the technical specifications and environmental requirements is imperative to selecting the appropriate materials that will ensure longevity and safety.
Furthermore, the quality and integrity of casing and tubing directly impact the economic viability of a well. Proper selection and maintenance of these components reduce operational risks and minimize the potential for costly repairs and environmental incidents. Therefore, their specification and inspection are governed by strict industry standards and regulations, ensuring that they meet the required thresholds for performance and safety.
In sum, casing and tubing are indispensable elements in drilling operations, each fulfilling distinct yet interconnected roles. The casing provides a protective barrier to the well, ensuring structural strength, while tubing serves as the pathway for hydrocarbons to reach the surface. The selection, installation, and maintenance of these components require a deep understanding of geological conditions, material science, and engineering principles. With advancements in technology and ever-evolving standards, the expertise required to effectively manage casing and tubing is continuously being elevated, underscoring their critical importance in the oil and gas industry. Understanding these differences not only aids in logistical planning but enhances the operational efficiency and safety of drilling endeavors.