Bull plugs are fundamental components in the oil and gas industry, designed to securely seal the ends of pipelines or tubular goods. This versatile tool is essential in preventing leaks and ensuring that systems operate smoothly and efficiently. To delve deeper into the intricacies of bull plug dimensions is to gain a clearer understanding of the vital role they play in maintaining the integrity of pipeline systems.

The dimension of a bull plug is crucial for its functionality. Typically, these components are available in a variety of sizes to accommodate different pipe diameters and pressure requirements. Most bull plugs are machined to fit standard pipe schedules, though custom dimensions are not uncommon, tailored to meet specific industry needs. The typical dimensions include the length, diameter, and thread type, each playing a crucial part in how the bull plug operates within a system.
A cornerstone of understanding bull plug dimensions is their thread type. The threads are critical as they allow the bull plug to be securely connected to the pipeline, ensuring that there are no leaks. The most common thread type for bull plugs is the NPT (National Pipe Thread), a U.S. standard for tapered threads used on threaded pipes and fittings. This thread type allows for a tight fit, which is pivotal in maintaining the pressure integrity of the pipeline.
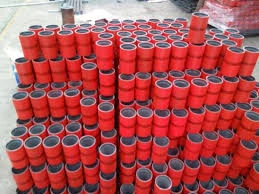
Another important dimension is the bull plug's diameter. The diameter must match the internal diameter of the pipe it is sealing. Standard diameters can range significantly, typically from 1/8 inch to over 20 inches. Selecting the correct diameter is essential for ensuring that the bull plug will effectively seal the pipe without risking damage to either the plug or the pipe itself.
The length of the bull plug is also worth noting. This dimension is less standardized and is usually determined by the specific application and the thickness of the pipe wall. A longer bull plug may be necessary for thicker pipes or those that need a more secure seal.
Materials used in bull plug construction greatly impact their dimensions and durability. Common materials include carbon steel, stainless steel, and brass. Each material offers different benefits; for instance, stainless steel bull plugs are known for their corrosion resistance, making them ideal for aggressive environments or offshore drilling. The material choice can influence the wall thickness of the bull plug, affecting its weight and the pressure it can withstand.
bull plug dimensions
The strength and quality of a bull plug are often determined by industry standards set by organizations like the American Petroleum Institute (API) or American Society of Mechanical Engineers (ASME). Conforming to these standards ensures that bull plugs can withstand the pressure and environmental conditions typical of oil and gas operations. These standards define not only the material requirements but also the dimensional tolerances that manufacturers must adhere to.
From an operational perspective, attention to bull plug dimensions plays a critical role in system maintenance and safety. Incorrectly sized bull plugs can lead to system failures, causing leaks, environmental hazards, or even catastrophic equipment failure. Therefore, selecting the correct bull plug dimensions is not just a matter of precision but also of safety and cost-effectiveness.
Professionals in the field often possess specialized expertise to recommend the appropriate bull plug for specific systems. This expertise is a combination of theoretical knowledge and hands-on experience in diverse operational scenarios. Experts may consider factors such as operating pressure, temperature, the fluid being transported, and the geographic location. Their recommendations are often backed by historical data, industry best practices, and cutting-edge technological advancements.
Industry advancements continue to improve the functionality and efficiency of bull plugs. Innovations such as advanced sealing technologies and materials that resist extreme temperatures and corrosive substances are gradually being integrated into bull plug designs. These advancements not only increase the reliability of the bull plugs but also extend the lifespan of entire pipeline systems, reducing the need for frequent replacements and maintenance.
Ultimately, bull plug dimensions are more than mere numbers; they are pivotal factors that underpin the successful operation of the oil and gas industry's complex pipeline systems. Through exacting standards, expert recommendations, and continual innovation, the oil and gas industry ensures that these components perform reliably under the most challenging conditions. The subtle nuances in dimension specifics highlight the importance of precision engineering and craftsmanship in the production and selection of bull plugs. Whether used for sealing an unused pipe port or for maintenance purposes, understanding and applying the correct bull plug dimensions is indispensable for the integrity and efficiency of oil and gas operations.