Bull plug pressure ratings are a critical aspect of wellbore integrity and oilfield operations. Understanding their importance and the factors affecting these ratings can significantly impact safety and efficiency in oil and gas extraction. With the rapid advancements in drilling technologies and the increasing complexity of wells, it is essential to have an expert understanding of bull plug pressure ratings to ensure operational success.
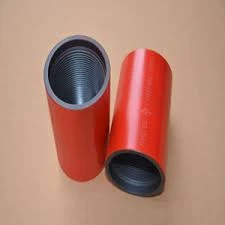
One of the core elements of bull plug pressure ratings involves the materials used in their manufacture. Typically made from high-grade steel or other durable alloys, bull plugs are designed to withstand intense pressure environments. The choice of material can directly influence the pressure rating, as each material has its strength limitations and resistance capabilities. Therefore, selecting the appropriate material is fundamental to ensure the bull plug's reliability and performance under pressure.
Pressure ratings are not arbitrary numbers; they are calculated based on rigorous testing and engineering standards. Organizations such as the American Petroleum Institute (API) have established guidelines and standards that dictate how pressure ratings are determined and certified. These standards ensure that bull plugs can perform safely under specific conditions, providing users with verified data on which to base their operational decisions.

It's also important to consider the environmental factors in which bull plugs are used. External conditions, like temperature and corrosive elements present in the wellbore environment, can affect the pressure rating. For instance, higher temperatures can weaken the material, thus reducing the effective pressure rating of the bull plug. Similarly, corrosive substances can degrade the material over time, leading to potential failures if not properly accounted for in the pressure rating.
The geometry and design of the bull plug play a significant role in its pressure rating. A well-designed bull plug will distribute stress evenly across its surface, minimizing the risk of weak points that could lead to a failure at high pressures. Advanced design techniques, including computer-aided simulations and finite element analysis, are employed to optimize the design of bull plugs, ensuring they can withstand the specific pressure scenarios they are likely to encounter.
Maintenance and inspection are integral to maintaining the pressure integrity of bull plugs. Regular inspections and testing should be conducted to detect any signs of wear or damage that could compromise the bull plug's pressure rating. Employing non-destructive testing techniques such as ultrasonic testing can help identify potential vulnerabilities without damaging the component.
bull plug pressure rating
Adhering to strict quality control measures during manufacturing is critical to ensuring that each bull plug meets its designated pressure rating. This involves performing rigorous testing during and after production to validate the plug's performance. Manufacturers with a reputation for excellence invest in state-of-the-art testing facilities and processes to guarantee that their products meet industry standards and exceed customer expectations.
Moreover, precise installation is necessary to assure the bull plug can perform to its rated pressure. Any misalignment or improper fitting can lead to increased stress concentrations, which might exceed the material's capacity, causing failures even at rated pressures. Training personnel in the correct handling and installation procedures can mitigate such risks.
With the industry’s shift towards sustainability and environmental considerations, there is a growing emphasis on the recyclability and environmental footprint of materials used in bull plugs. Using materials that are not only high-performing but also environmentally sustainable can contribute to greener operations without compromising on safety and performance.
Investing in a higher-rated bull plug might seem like an unnecessary cost to some operators, but the trade-off often lies in increased safety margins and reduced risk of failure. This can lead to significant savings by avoiding costly repairs or environmental cleanups resulting from wellbore failures.
Ultimately, the choice of a bull plug with the appropriate pressure rating is not merely a technical decision but a strategic one. It involves balancing the operational demands with safety considerations, cost factors, and long-term reliability, underscoring the need for expertise and authoritative guidance in selection and application.
In conclusion, bull plug pressure ratings are crucial for successful and safe oilfield operations. By integrating stringent standards, innovative design, and meticulous maintenance, operators can ensure that their wells remain stable and productive. Through continuous advancements and adherence to best practices, the oil and gas industry can meet the challenges of today’s drilling environments with confidence and integrity.