such as bull plug vs hex plug often encounter in discussions related to industrial applications and plumbing solutions. These two types of plugs, although appearing similar, serve distinct purposes, with each offering its unique set of benefits across various applications. Drawing from experience and expert knowledge, we delve into a comparative analysis of bull plugs and hex plugs, dissecting their uses, advantages, and the circumstances under which one might be favored over the other.
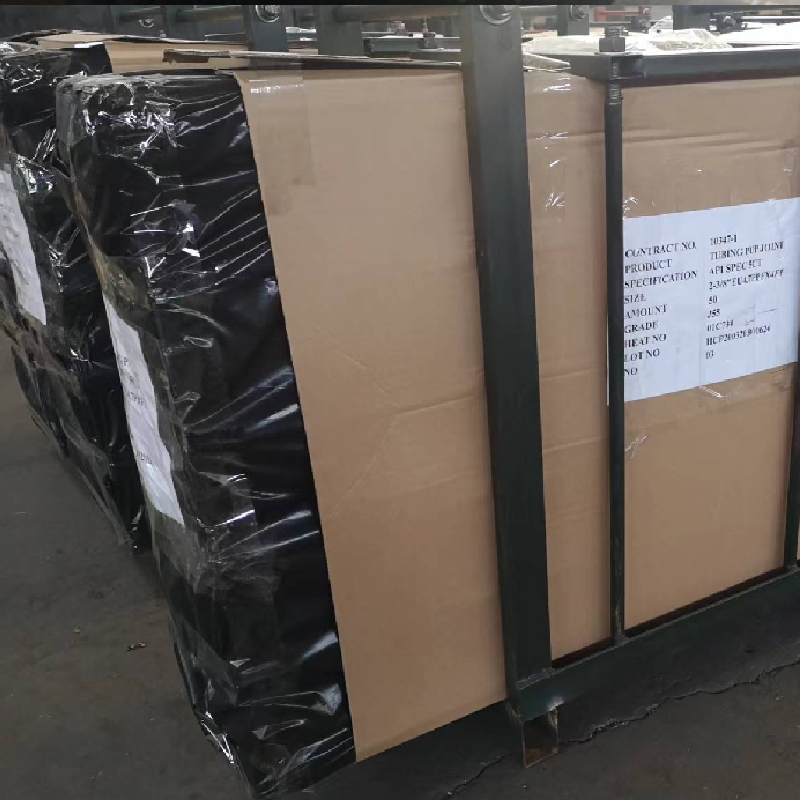
Bull plugs, frequently utilized in the oil and gas industries, are designed to seal the ends of pipes. This robust component typically features a tapered male thread and a rounded closed end, allowing for secure blockage of fluid flow in pipelines.
The design and construction of bull plugs allow them to excel in high-pressure environments where standard plugs might fail. Their application is particularly crucial in operations where maintenance and modifications necessitate temporary stoppage in a pipeline system. The bull plug’s ability to withstand high temperature and pressure makes it indispensable for industries where the reliability and safety of the equipment are paramount.
The hex plug, on the other hand, is characterized by its hexagonal head, which facilitates easier installation and removal using standard tools such as wrenches. These plugs offer a practical solution for sealing pipe connections where ease of access and manipulation are essential. Given their typically small footprint, hex plugs are versatile and are widely used in plumbing, automotive, and heating systems. They allow for quick sealing solutions and demonstrate high resistance to leakage in lower pressure applications compared to their counterparts. The design of the hex plug facilitates its use in tight spaces, a feature that is intriguingly beneficial in complex piping systems or where regular disassembly is required.

When comparing bull plugs to hex plugs, it is vital to consider the operational environment and specific requirements of the task at hand. For applications that demand robust sealing under extreme conditions, bull plugs are the preferred choice. Their durability and pressure resistance make them exemplary in scenarios where failure is not an option. Conversely, hex plugs are more suited for general sealing tasks, particularly in environments where ease of use and quick access are vital. Their design optimally balances efficiency with accessibility, offering a practical solution without overengineering tasks that do not require the industrial strength provided by bull plugs.
bull plug vs hex plug
Industry professionals with years of experience can attest to the importance of selecting the appropriate plug for each specific circumstance. One might opine that the decision between a bull plug and a hex plug ultimately boils down to the balance between strength and convenience. Notably, the distinction becomes clear within the context of operation sizes and scales—a testament to their tailored functionality.
Advancements in materials and design have also played a significant role in enhancing the performance of both bull and hex plugs. Modern manufacturing techniques utilize advanced composites and alloys to make these components lighter yet stronger, improving overall efficiency. This innovation further reinforces the need for expertise in selecting the correct plug type, as the choice can profoundly affect operational safety and efficacy.
Reliability, therefore, emerges as a crucial factor in determining the choice of plug. Bull plugs, with their robust constitution, offer high reliability in pressure-intensive and extreme environments. Hex plugs, due to their ease of manipulation and installation, are highly reliable in common plumbing and engineering applications. Each plug possesses intrinsic properties that render it reliable, contingent upon its intended purpose.
Thus, the exploration of bull plug vs hex plug underscores a comprehensive appraisal of need-based application over generalization. Through nuanced understanding and expert insight, the adoption of the right component ensures optimized performance, safety, and productivity in industrial operations. With continuous innovation, the future of these essential components promises even greater adaptability and functionality, remaining integral to evolving industry standards and needs.