In the field of industrial applications, particularly within the oil and gas industries, the debate over the most effective types of plugs—bull plug versus round head plug—has persisted. Each serves the purpose of sealing different piping systems, yet differences in their design and application often make one more suitable than the other depending on specific operational needs. Understanding these differences is crucial for professionals aiming to enhance system integrity and efficiency.
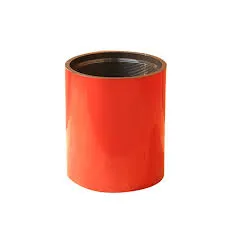
The bull plug, named for its robust design, resembles a bull's head in its structure. It features a threaded male end and is typically employed in the ends of pipes or tubing to close off unused sections of the piping system. These plugs are often made from high-quality materials such as stainless steel or carbon steel, enabling them to withstand high pressures and temperatures. Bull plugs are particularly favored in applications where durability and reliability are paramount. Their design ensures a secure fit that minimizes the risk of leaks, which is critical in high-stakes environments like offshore drilling platforms.
Moreover, bull plugs' resistance to corrosion makes them a preferred choice in environments where exposure to harsh elements is inevitable. According to industry experts, regularly inspecting the integrity of bull plugs is essential. Ensuring that the threads remain in good condition and free from wear can prevent potential failures, enhancing system longevity and safety.
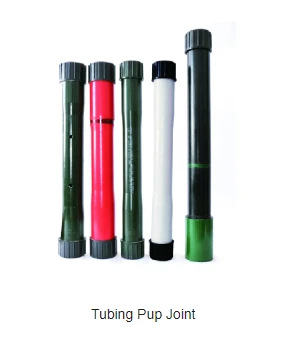
On the other hand, round head plugs possess a more simplistic design but with distinctive features that make them ideal for certain applications. Unlike bull plugs, round head plugs have a smooth, round end and are generally used in situations where a more moderate seal is acceptable. Though typically constructed from similar materials to bull plugs, such as stainless steel, round head plugs are often used in applications where aesthetics and ease of installation are more pressing concerns than extreme durability.
bull plug vs round head plug
In terms of professional expertise, selecting between a bull plug and a round head plug should involve a consideration of both the application's environmental conditions and the specific demands of the pressure system. While bull plugs might offer superior sealing capabilities in high-pressure systems, round head plugs can be more appropriate for controlled environments like process plants, where visual inspection and ease of access are critical.
Professionals with extensive field experience stress the importance of understanding the specific requirements of any given project before making a material choice. Misapplication of either plug type can result in significant operational setbacks, including leakage and premature system failure. Therefore, consulting with a certified engineer or a seasoned field technician can provide invaluable insights into the optimal choice for any given situation.
Moreover, maintaining a database of various operational projects and their results when using either plug type can enrich a company's understanding and anticipation of future needs. Continual learning and adaptation in plug selection align with best practices and advances in plug design and material technology.
In conclusion, while bull plugs offer unmatched durability and pressure resistance suited for the most rigorous industrial applications, round head plugs provide a viable solution for less demanding conditions where ease of use and aesthetic considerations are prioritized. By leveraging expertise, rigorous field testing, and a comprehensive understanding of system needs, professionals can ensure the correct plug type is selected, thus maintaining the integrity and efficiency of piping systems across diverse applications.