In the intricate realm of the oil and gas industry, the term bull plug is one that resonates with those who seek efficiency and reliability in their operations. A bull plug is a critical component designed to cap off the ends of pipes within the oil field, providing a secure seal and ensuring optimal control over the flow within the drilling systems. Understanding its usage and significance is crucial for any entity involved in this highly technical field.
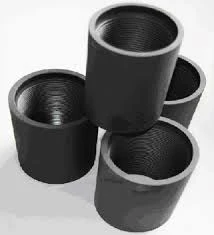
The role of a bull plug in securing oil and gas operations cannot be understated. These devices are typically manufactured from high-strength steel or alloys to withstand the extreme pressures and corrosive environments encountered in drilling operations. The primary function of a bull plug is to provide an end point or closure to a pipe, preventing leaks and maintaining the integrity of the system under high-pressure conditions. By employing bull plugs, operators can ensure that their tools and equipment perform efficiently without unexpected interruptions.
Quality control in the manufacturing of bull plugs is a testament to the commitment towards excellence within the oil and gas plumbing infrastructure. Manufacturers adhere to stringent industry standards such as API (American Petroleum Institute) guidelines to guarantee that every bull plug delivers superior performance. Ensuring that these components have the correct mechanical properties, such as tensile strength and pressure ratings, is vital for maintaining consistent operations in challenging environments.

One of the distinguishing features of an exceptional bull plug is its ability to provide a reliable seal even when exposed to substantial temperature fluctuations. Operators often look for bull plugs with robust threading patterns and enhanced sealing capacities, which are tested under controlled conditions to mimic real-world scenarios. This attention to detail is critical in fostering trust and reliability, which directly contributes to the overall safety and efficiency of drilling projects.
Moreover, the selection of material for bull plugs is pivotal. Materials such as carbon steel, stainless steel, and various high-strength alloys are evaluated based on their resistance to the elements present in the oil extraction process, including chemicals and high pressures. The right choice of material helps extend the lifespan of the bull plug, reducing the frequency of replacements and minimizing operational costs.
bull plug oil and gas
In terms of application versatility, bull plugs are utilized across various stages of oil and gas drilling—from the initial setup to routine maintenance activities. Their integration into different operational contexts exemplifies their indispensable nature. The ability to easily install and replace bull plugs without disrupting ongoing operations enhances the operational efficiency and flexibility of field operators.
Training and experience play a significant role in the correct implementation of bull plugs in the field. Technicians and engineers equipped with knowledge about the latest advancements and proper installation techniques contribute to the seamless integration of the bull plug into the system, ensuring that the equipment performs as expected. Regular training sessions and certifications ensure that personnel remain updated with industry trends, further reinforcing the credibility and reliability of the operations.
The availability of comprehensive documentation from manufacturers detailing the specifications, installation guidelines, and maintenance procedures of bull plugs further supports their authoritative presence in the market. This documentation not only provides critical insights into product capabilities but also assists users in making informed decisions based on specific operational needs.
The robustness of bull plugs directly impacts their role in preventing potential environmental hazards. By effectively sealing the pipeline, these components help mitigate the risk of oil spills and leaks, which could have devastating effects on the environment. The adoption of environmentally-friendly practices through the use of reliable sealing technologies underscores the industry's commitment to sustainable operations.
In conclusion, the use of bull plugs in the oil and gas industry epitomizes a convergence of expertise, reliability, and continuous innovation. Their critical role in ensuring system integrity and operational efficiency cannot be overstated, making them indispensable in the realm of drilling technology. In a sector that demands both precision and durability, the bull plug stands as a beacon of engineering prowess, supporting the pursuit of safer and more efficient energy extraction.