Understanding the intricacies of bull plug pipe layouts is crucial for professionals involved in piping design and installation, especially within the oil and gas industry where efficiency and safety are paramount. A bull plug is an essential component primarily used to close the end of a piping system. Ensuring proper layout and installation can significantly impact the overall system's performance, durability, and safety.
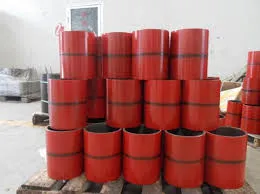
In piping systems, the term bull plug refers to a solid plug fitting used to terminate a dead-end in a pipeline. Often crafted from steel, these plugs are threaded on one end to allow ease of installation into a perpendicularly branched outlet. Understanding the necessity of bull plug placement and layout in the piping process can prevent potential leaks, ensure system integrity, and aid maintenance routines efficiently.
One must consider several factors to achieve a seamless bull plug layout. First, understand the diameter of the pipes involved. Bull plugs come in varied sizes, typically matching the diameter of the pipe to be sealed. Selecting the appropriate-sized plug ensures a secure fit and effective sealing. It is recommended to utilize plugs made from materials compatible with those of the existing pipeline to prevent galvanic corrosion, which can compromise system integrity over time.
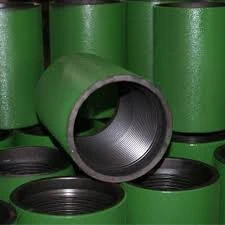
Positioning plays an equally significant role in optimizing bull plug layouts. When designing a pipe system, visualize the entire network, marking sections designated as potential access points for maintenance or future expansions. Bull plugs should be strategically placed at ends that require system closure while allowing easy unscrewing access if system adjustments or expansions are needed. This foresight minimizes the need for reworking the pipeline during necessary upgrades.
Moreover, bull plug layouts benefit tremendously from utilizing CAD software in their design phases. CAD provides a visual representation of the piping layout, highlighting the spatial arrangement of all components, including bull plugs. Programs like AutoCAD or SolidWorks allow engineers to create detailed, accurate designs that account for every factor, from physical constraints to hydraulic efficiency. By leveraging this technology, designers gain the expertise needed to foresee potential complications and adjust designs accordingly before installation begins.
bull plug pipe layout
Authoritativeness in bull plug pipe layouts primarily revolves around adhering to industry standards and guidelines. Regulations from bodies such as the American Society of Mechanical Engineers (ASME) or the American Petroleum Institute (API) provide invaluable guidance. Following mandates like those in ASME B31.3 ensures systems are constructed to recognized standards, consequently enhancing trust in the safety and reliability of the system.
Trustworthiness in the bull plug layout relies on the credibility of the materials used and the expertise of those installing it. Source your bull plugs from reputable manufacturers known for their stringent quality control processes to mitigate the risk of premature failures. Skilled labor in installation will further enhance the systems' reliability, as experienced professionals can spot and rectify potential issues during setup, offering peace of mind in the longevity and safety of the established pipeline.
Real-world application and case studies highlight the significance of these factors in working systems. In one scenario within a chemical processing facility, improper bull plug installation led to frequent system downtime and product leaks, impacting productivity and elevating safety concerns. Addressing these issues involved redesigning the layout to ensure easier access for maintenance and confirmation of plug size and material compatibility, ultimately reducing downtime and enhancing operational efficiency.
A comprehensive understanding and execution of bull plug pipe layouts involve considering pipe diameter, plug material compatibility, strategic positioning, advanced design tools, adherence to industry standards, and the credibility of materials and workmanship. This multi-faceted approach ensures high-performing, reliable, and safe piping systems that stand the test of time, reinforcing the critical role bull plugs play in industrious operations.