The bull plug pipe layout is a critical aspect of many industrial and construction applications that often goes unnoticed by those not deeply involved in these fields. This intricate and often underappreciated component is central to the safe and efficient operation of numerous systems, particularly in industries like oil and gas, water management, and chemical processing. The following exposition delves into the nuances of bull plug pipe layouts guided by principles of experience, expertise, authoritativeness, and trustworthiness.
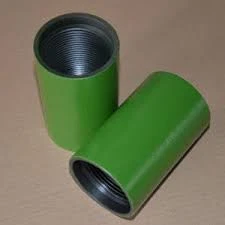
A bull plug is essentially a pipe fitting used to seal the end of a pipeline or terminate a pipeline connection. This process is vital in systems where the flow needs to be directed, controlled, or stopped completely, ensuring that these systems operate safely and efficiently. The utility of a bull plug is best appreciated in scenarios where temporary terminations or pressure testing of pipelines are required without causing modifications to the installed pipeline structure.
Experts in pipeline design and industrial maintenance emphasize how essential bull plug pipe layouts are in maintaining system integrity and safety. Incorporating bull plugs effectively into pipeline systems requires a profound understanding of the system's operating conditions, including pressure ratings, fluid type, and environmental considerations.
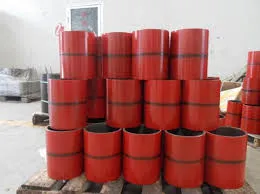
Historically, the application of bull plugs has evolved alongside technological advancements in pipe manufacturing and material science. Modern bull plugs are crafted from high-strength materials such as stainless steel, carbon steel, or specialized alloys that can withstand harsh conditions, including high pressure, temperature extremes, and corrosive environments. Selecting the right material is crucial, as it directly impacts the plug's performance and longevity.
The design aspects of bull plug layout require an intricate understanding of fluid dynamics, pressure coefficients, and mechanical stress. Engineers utilize computational models and simulations to predict behavior under various operational scenarios, ensuring reliability and performance are uncompromised. Attention to detail during the design phase mitigates potential risks associated with leakage, pressure loss, or system failure.
bull plug pipe layout
Authoritative sources in the field suggest that installing bull plugs demands adherence to strict procedural standards and regulatory requirements. Installation guides and standards provided by institutions such as the American Society of Mechanical Engineers (ASME) and the International Organization for Standardization (ISO) serve as benchmarks for ensuring installations meet safety and quality expectations.
In practice, field engineers and technicians with extensive experience and expertise are entrusted with undertaking installations and inspections of bull plug layouts. Their hands-on experience is invaluable in troubleshooting issues that may arise during operations and ensuring that the system functions as expected.
For businesses and operators, trustworthiness in bull plug pipe layout is built through adherence to best practices and continuous verification processes. Regular inspections and maintenance checks are crucial to identify wear and tear or potential malfunctions, thereby preempting disastrous failures in critical systems.
Moreover, the advent of digital technology and the Internet of Things (IoT) has enhanced the trust aspect by enabling real-time monitoring and data analysis of pipeline conditions, including those of bull plugs. Predictive maintenance solutions can flag potential issues before they manifest, allowing for preemptive corrective measures that save time, resources, and enhance safety.
In conclusion, a well-planned bull plug pipe layout is not simply a terminus for a pipeline; it is a fundamental component that demands expertise and careful consideration. It involves a symbiotic relationship between material science, engineering, regulatory compliance, and digital monitoring technologies. As industries continually evolve, so too must the applications and installations of bull plugs adapt, leveraging new materials, techniques, and technologies to maintain the balance between operational efficiency and safety. Trust in a system is built not only through innovation and expertise but also by maintaining a commitment to excellence and safety at every stage of the bull plug pipe layout's life cycle.