Exploring the Versatility and Strength of Bull Plugs for Industrial Applications
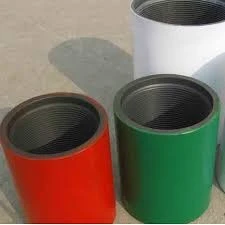
In the rugged landscape of industrial equipment, where resilience and reliability take precedence, bull plugs stand out as indispensable components. While these seemingly simple devices might not capture immediate attention, their functionality and versatility earn them a crucial role in various sectors, especially in piping systems and oil and gas industries.
A bull plug, essentially a cylindrical, threaded pipe fitting, is designed to seal off the end of a pipe. It's crafted to withstand extremely high pressures, making it vital for maintaining safety and efficiency in pipeline operations. Among the many materials used for manufacturing bull plugs, carbon steel, stainless steel, and alloy steel are preferred for their strength and durability.
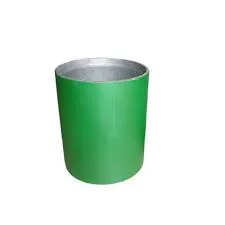
From an experiential perspective, users often commend bull plugs for their ease of installation and robust construction. In industries where time and safety are paramount, the quick and secure installation of a bull plug can prevent delays and avert potentially hazardous leaks. In fact, experienced engineers frequently recommend incorporating bull plugs during pipeline design to facilitate routine maintenance and pressure testing, highlighting their practical benefit to operational workflows.
bull plugs
On the expertise front, understanding the precise specifications of bull plugs is crucial. These specifications include factors like pressure ratings and temperature compatibility, which vary based on application requirements. Industry professionals emphasize the importance of selecting the correct bull plug to match the pipe's material and fluid type, preventing corrosion or wear over time. Additionally, the threading on bull plugs, namely the NPT (National Pipe Thread) standard, ensures a tight, secure fit, minimizing the risk of leaks under high-pressure scenarios.
Connecting expertise with authoritativeness, the safety standards governing bull plugs reflect their significance in industrial use. Widely accepted codes, such as those from the American Society of Mechanical Engineers (ASME) and the American Petroleum Institute (API), set rigorous benchmarks for these components, ensuring they meet stringent safety requirements. Compliance with these standards is not merely a recommendation but a necessity to maintain operational integrity and safeguard against pipe failure incidents.
However, trustworthiness in the use of bull plugs goes beyond compliance. Trust is fortified through thorough testing and quality assurance processes undertaken by manufacturers. Leading brands in the industry often subject their bull plugs to rigorous inspections, including hydrostatic and nondestructive testing, to ensure they perform as expected under operational stress.
In conclusion, the significance of bull plugs in industrial applications cannot be overstated. Their practical benefits, coupled with expert endorsements and adherence to authoritative safety standards, underline their indispensable role in maintaining the safety and efficiency of pipeline systems. Whether confronting extreme pressures in oil extraction or ensuring the seamless flow of liquids in manufacturing, bull plugs prove to be a logical and trusted choice for engineers and industry professionals seeking reliable sealing solutions.