In the realm of industrial piping and plumbing solutions, the selection of appropriate components can significantly influence the efficiency and safety of the system. Two common components that often spark debate among industry professionals are bull plugs and hex plugs. A deep dive into their applications, structural differences, and material considerations can help ensure that the right choice is made for specific needs.
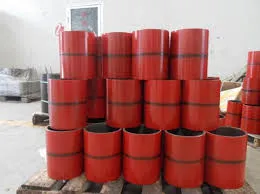
Bull plugs and hex plugs, although similar in their fundamental purpose of sealing off pipe ends, exhibit distinct characteristics that define their uses and suitability for different industrial tasks. Understanding these differences not only ensures operational efficiency but also maintains safety standards across various applications.
Bull plugs are typically utilized in situations that demand the temporary or permanent sealing of pipework sections. Constructed with a solid, rounded body, bull plugs are often employed in high-pressure systems due to their robust design. This makes them ideal for industries like oil and gas, where they serve as integral components in capping wells and test pipes. Their design also facilitates easy insertion and removal, which is crucial during maintenance procedures or when pressure testing is required.

On the other hand, hex plugs are named for their hexagonally shaped heads, which enable easy installation and uninstallation with standard wrenches. The design of hex plugs caters to situations that do not demand high pressure endurance but require frequent access or adjustments. Their versatility makes them a staple in industries ranging from automotive to residential plumbing, where they are used to seal off open pipe sections temporarily for service or repair. The ease of use and accessibility offered by the hexagonal design significantly streamlines the processes, minimizing downtime and enhancing productivity.
Material selection plays a pivotal role in deciding between a bull plug and a hex plug. Both components are available in a range of materials, including stainless steel, brass, and carbon steel, each offering specific advantages depending on the required application. For instance, stainless steel variants offer superior resistance to corrosion, making them highly suitable for harsh environmental conditions typical in offshore drilling applications. Conversely, brass components provide excellent thermal conductivity and are often utilized in water supply systems where temperature fluctuations are prevalent.
bull plug vs hex plug
Furthermore, the threading of these plugs is a critical consideration. Ensuring compatibility between the plug and the pipe threading guarantees a secure seal that mitigates leakage risks. Common thread types include National Pipe Thread (NPT) and British Standard Pipe (BSP), and the choice between them should be dictated by the existing system specifications and industry standards.
From a maintenance perspective, the choice between bull plugs and hex plugs can influence the operational uptime and the ease of compliance with safety regulations. Bull plugs, with their robust build, tend to require less frequent replacements, thus offering a cost-effective solution over time. Hex plugs, while easier to replace, may necessitate regular inspection to ensure the integrity of the seal. This difference significantly impacts the decision-making process, especially in industries where continuous operation is paramount.
In conclusion, the debate between using a bull plug versus a hex plug is contingent upon a comprehensive understanding of the operational environment, the expected pressure loads, and material suitability. Industrial and plumbing experts must weigh the nuances of each option to align with project-specific requirements and safety protocols. By approaching the decision with well-rounded expertise and thorough evaluation of both the structural and material aspects, professionals can enhance system reliability and optimize performance.
Choosing between a bull plug and a hex plug is not merely a matter of preference but a calculated decision that involves considering the interaction of various factors. Expert knowledge and authority on the subject, underpinned by real-world experience, lead to informed decisions that uphold the credibility and trustworthiness essential in industrial operations. Such informed choices not only contribute to operational success but also reinforce the overarching commitment to safety and sustainability in engineering solutions.