Casing coupling dimensions play a critical role in the oil and gas industry, ensuring the structural integrity of well-casing connections. These dimensions dictate the compatibility and performance of casing joints, which are essential for maintaining wellbore integrity in varying subsurface conditions.
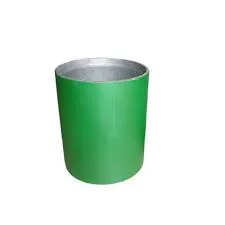
From the perspective of experience, the selection of appropriate casing coupling dimensions is an exercise informed by decades of field operations and the nuanced understanding of geological pressures. Operators must account for diameter, wall thickness, and grade of the coupling to safeguard against well collapses and ensure longevity of the infrastructure. Real-world scenarios underscore the importance of precision. In one noted instance, a miscalculation of dimensions led to casing failure in a high-pressure well, causing costly downtime and repair.
This experience amplifies the necessity for exact measurements in coupling designs.
Expertise in casing coupling dimensions stems from a comprehensive grasp of mechanical engineering principles and materials science. Engineers must consider the enormous stress loads and thermal cycling that casing joints endure. Advanced tools like 3D modeling software and finite element analysis are employed to predict performance outcomes. For instance, understanding the yield strength of coupling materials, such as carbon or alloy steels, informs the selection process to prevent deformation under stress. Moreover, expertise influences the customization of couplings for specific project conditions, optimizing both cost-effectiveness and resilience. Seasoned professionals consult detailed standards such as those provided by the American Petroleum Institute (API), which set a benchmark for coupling dimensions and tolerances.
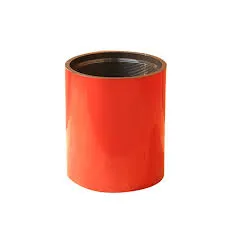
casing coupling dimensions
The authority of a reliable source on casing coupling dimensions is reinforced through adherence to international standards and an extensive track record within the industry. Companies that consistently deliver casing couplings in compliance with API 5CT and ISO 11960, while surpassing these standards in proprietary testing, establish themselves as leaders. Authoritative organizations conduct rigorous testing including tensile, hydrostatic, and collapse tests, ensuring each coupling can handle extreme conditions encountered during drilling and production. Additionally, post-manufacture, each coupling undergoes quality assurance processes such as non-destructive testing methods to certify integrity. Companies partnering with these industry stalwarts gain not only premium products but also invaluable technical support from experts who contribute to standardization committees.
Trustworthiness in the field of casing coupling is paramount, as errors can jeopardize projects and safety. Transparency in material sourcing, manufacturing processes, and compliance certifications builds confidence among operators and stakeholders. For instance, product traceability is crucial; each coupling's production journey, from raw material to final inspection, is meticulously documented. This transparency not only ensures quality but also provides a foundation for swift issue resolution should problems arise in the field. Trust is further nurtured by providing warranties and guarantees that underline the manufacturer's confidence in their product's durability and performance.
In conclusion, the topic of casing coupling dimensions encompasses a blend of detailed technical knowledge, adherence to rigorous standards, and the cultivation of trust through transparency and experienced application. The mastery of these elements ensures that the final product not only meets but exceeds the demands of its application, thereby securing the reliability and efficiency of well operations across the globe.