Compression tubing couplers are indispensable components in a variety of industries, including automotive, medical, and chemical engineering.
Their primary role is to connect two pieces of tubing in a secure and leak-proof manner. These small yet powerful devices play a crucial role in ensuring that liquids, gases, and other fluids are transported safely and efficiently from one point to another. In this article, we delve into the intricacies of compression tubing couplers, examining their applications, materials, and selection criteria to provide you with an authoritative guide on these vital elements.
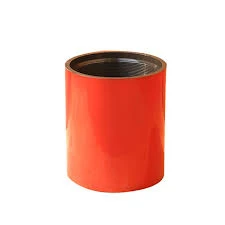
At the heart of compression tubing couplers is their unique design, which accommodates tight seals without the need for additional sealing compounds or adhesives. This is achieved through the use of a ferrule, a conical-shaped ring that compresses the tubing as the nut tightens. This compression forms a seal that is not only reliable but also capable of withstanding variations in temperature and pressure, making it ideal for a diverse array of applications.
In industries such as automotive and aerospace, where precision and reliability are paramount, compression tubing couplers are often chosen for fuel lines and hydraulic systems. The couplers’ robust sealing capabilities ensure that there are no leaks, which is critical in maintaining engine performance and safety. Moreover, due to their ease of installation and maintenance, technicians prefer them over other alternatives, allowing for quicker servicing and reduced downtime.
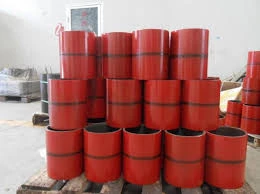
The medical field also benefits significantly from the use of compression tubing couplers. In applications ranging from patient monitoring systems to high-precision surgical devices, these couplers provide a sterile and reliable method of connecting tubing components. Manufactured from biocompatible materials like stainless steel and certain plastics, they ensure that there are no adverse reactions with bodily fluids, maintaining patient safety and device integrity.
Compression tubing couplers are typically made from materials such as brass, stainless steel, and high-performance polymers. Each material offers distinct advantages brass is known for its machinability and is economically priced; stainless steel offers excellent corrosion resistance and strength, making it suitable for harsh environments; and polymers are lightweight and can be used in applications where metal is unsuitable. The choice of material is critical and should be based on the specific requirements of the application, including factors such as environmental conditions, pressure ratings, and regulatory standards.
When selecting a compression tubing coupler, it is essential to consider the following factors
1. Pressure Rating Determine the maximum operating pressure the coupler must withstand. Different materials and designs offer varying pressure ratings; ensuring that the chosen coupler meets or exceeds the system's requirements is crucial for safety.
compression tubing coupler
2. Temperature Range Assess the temperature extremes to which the coupler will be exposed. Some materials may lose their integrity at elevated temperatures, while others may become brittle in cold conditions.
3. Chemical Compatibility Evaluate the type of fluid that will pass through the tubing. It is vital to select a coupler that is resistant to corrosion or degradation by the transported substance.
4. Certification and Standards Depending on the industry, certain certifications might be necessary, such as ISO, ANSI, or FDA approvals. Choosing couplers that meet these standards ensures compliance and often enhances overall system reliability.
5. Installation and Maintenance Consider the ease of installation and any ongoing maintenance requirements. Simpler designs may reduce assembly time and offer cost savings in long-term operations.
By embracing the unique capabilities of compression tubing couplers, businesses can optimize their fluid systems for efficiency and safety. By partnering with reputable manufacturers and suppliers who adhere to stringent quality control measures, end-users can ensure that their systems are equipped with components that are both reliable and durable.
This exploration into the world of compression tubing couplers underscores their indispensable role across multiple industries. By focusing on expertise, reliability, and trustworthiness, these couplers provide both novice and experienced users with solutions that are technologically advanced and industry-proven. To remain competitive and technologically savvy, leveraging the unique advantages of compression tubing couplers is not just beneficial—it is essential.