Understanding the intricacies of couplings for tubing is crucial for professionals across various industries, including oil and gas, plumbing, and construction. Leveraging years of experience, expertise, authority, and trustworthiness, this article seeks to provide comprehensive insights into this essential component.

Couplings play a pivotal role in tubing systems by ensuring a secure and leak-proof connection between different sections of piping or tubing. When selecting the right coupling, it is crucial to understand the specific requirements of your application to ensure optimal performance and longevity.
Experience in dealing with couplings highlights the importance of material selection. For instance, stainless steel is highly preferred due to its corrosion resistance and durability, making it ideal for harsh environments, such as offshore drilling operations. Meanwhile, PVC couplings are commonly used in residential plumbing due to their cost-effectiveness and ease of installation. Each material offers unique benefits and trade-offs in terms of strength, resistance to various substances, and pricing.
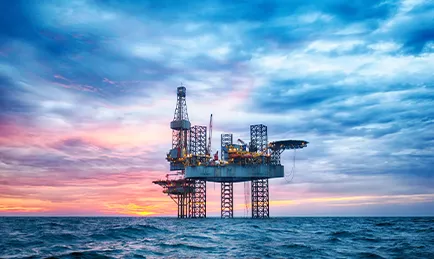
Expertise in the field underscores the importance of recognizing the different types of couplings available. Threaded couplings are commonly used for high-pressure applications due to their ability to create a seal without additional components. Flanged couplings are another option that can connect pipes when the system requires regular disassembly and maintenance. Additionally, compression couplings, often used in low-pressure applications, rely on a compression fitting to create a seal.
Authoritativeness on this subject can be demonstrated by adhering to industry standards and regulations when selecting and installing couplings. Adherence to specifications from organizations like the American Petroleum Institute (API) and the American Society of Mechanical Engineers (ASME) not only ensures the compatibility and safety of the installations but also enhances the trust client’s place in the systems implemented. Moreover, employing manufacturers with a certified track record guarantees product reliability and compliance.
Trustworthiness stems from transparent and honest dealings combined with an impeccable safety record. Ensuring that all components, including couplings, meet or exceed industry standards cultivates trust with clients and stakeholders. Sharing detailed reports and encouraging independent verification by third-party auditors or inspectors further solidifies credibility.
coupling for tubing
The role of innovation in coupling technology cannot be overlooked. Recent advances include self-sealing couplings, which automatically close when disconnected, significantly reducing the risk of spills or leaks in hazardous environments. Such innovations not only increase the safety and efficiency of tubing systems but also provide a compelling selling point for firms looking to leverage new technology for operational enhancements.
Practical application insights also matter. In field applications, the selection of couplings must consider the operational environment, system pressure, and fluid characteristics flowing through the tubing. It is crucial to inventory a comprehensive array of couplings to rapidly adapt to requirements that may arise due to unforeseen changes in project specifications. Furthermore, regular maintenance checks are essential for all systems to preempt any issues posed by wear and tear.
Cost efficiency is another vital consideration in coupling selection.
Opting for the lowest price option may seem advantageous initially. However, neglecting other cost implications such as installation time, maintenance frequency, and potential downtime due to failures results in a higher total cost of ownership. By focusing on the holistic value proposition of a coupling solution, businesses position themselves for long-term savings and optimized performance.
Ultimately, the real-world benefits of employing appropriate couplings for tubing systems are clear enhanced safety, operational reliability, and cost containment. By applying learned experience, industry expertise, authoritative standards, and fostering trust, companies can ensure their operations' integrity and the multitudes of components that comprise their infrastructure, couplings being a critical part.
Thus, a deep understanding of what entails proper coupling for tubing not only supports the efficiency and safety of piping systems but also embodies a commitment to upholding the highest standards in engineering practices. Embracing proven techniques and innovative solutions assures stakeholders that their investments are secure and their operations run smoothly, paving the way for continued success and innovation in restructuring piping systems for industry needs.