Drill pipe crossovers serve as the unsung heroes in the complex world of drilling, acting as pivotal connections that ensure seamless transitions between various thread configurations. With the ever-evolving demands of the oil and gas industry, choosing the right crossover can make or break the success of a drilling operation.
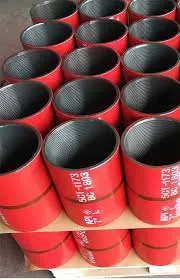
Imagine tackling a challenging deepwater project where equipment compatibility issues could lead to costly delays. Opting for high-quality drill pipe crossovers manufactured from premium materials such as AISI 4145H or AISI 4140 alloy steel ensures durability and reliability even under the most strenuous conditions. These materials are chosen for their impressive tensile strength and resistance to impact, qualities indispensable in high-stress drilling environments.
The configuration of drill pipe crossovers often specifies their utility, necessitating expertise in thread compatibility. A drilling specialist with years of experience can corroborate that understanding the nuances of API, premium,
and custom threading is crucial. This ensures proper torque application and seal integrity, which are vital for maintaining operational success and safety standards. API connections such as NC (numbered connections) are widely adopted, whereas premium threads might be required for high-pressure, high-temperature (HPHT) environments. Trust in these configurations is reinforced by their compliance with rigorous industry certifications, which serve as a testament to their quality and reliability.
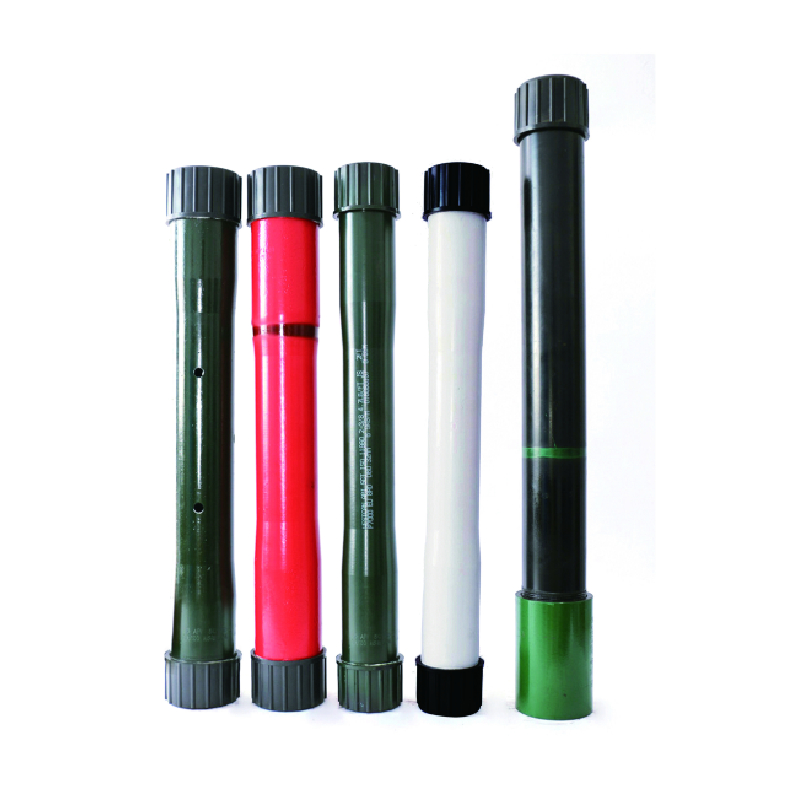
Furthermore, drill pipe crossovers play a significant role in the operational adaptability of drilling rigs. The flexibility offered by crossovers allows for the utilization of existing equipment across multiple projects without the need to invest in new tools for every job. This adaptability not only minimizes equipment expenditure but also reduces operational downtime, underscoring the financial prudence of selecting the proper crossovers for diverse drilling scenarios.
drill pipe crossover
Moreover, ensuring operational longevity is paramount, where maintaining a detailed log of crossover usage and rotation is recommended by seasoned industry veterans. This practice helps mitigate wear and tear, thereby extending the lifecycle of the equipment. In addition to regular checks for signs of fatigue or stress fractures, adherence to an established maintenance schedule increases the reliability and safety of drilling operations.
In the perspective of environmental stewardship, choosing the right drill pipe crossovers also contributes to minimizing ecological impacts. By ensuring secure and leak-free connections, there is a reduced risk of spillage or blowouts, which could have disastrous environmental consequences.
In conclusion, drill pipe crossovers are indispensable components necessitating informed decision-making backed by experience and technical know-how. Their contribution to operational success, cost efficiency, and environmental safety cannot be overstated. Selecting high-quality, meticulously engineered crossovers embodies a company's commitment to excellence and responsibility in the challenging field of drilling.