Female threaded couplings are an integral component in various industrial and plumbing applications, providing secure connections between pipes and ensuring optimal fluid or gas transportation. These couplings are characterized by their female threads, designed to mate with male-threaded pipes or fittings, offering a tight seal and reliable joint for efficient fluid conveyance.
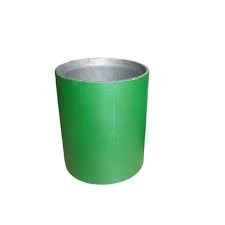
A host of industries leverage female threaded couplings due to their reliability and versatility. In plumbing, they serve as vital connectors in residential, commercial, and industrial settings, facilitating the routing of water, gas, and other essential fluids. Many sectors, such as oil and gas, chemical processing, and water treatment, depend on the robustness and adaptability of these couplings.
The materials used in manufacturing female threaded couplings significantly influence their performance and longevity. Commonly, these couplings are crafted from durable metals such as stainless steel, brass, and galvanized steel, each providing varying degrees of corrosion resistance, strength, and temperature tolerance. Stainless steel couplings, for example, are favored in environments where high resistance to corrosive agents and extreme temperatures is vital. Brass, known for its antimicrobial properties, is often used in systems involving potable water.

Precision in threading is crucial in the manufacturing process, as it ensures that the coupling effectively engages with the corresponding male threads of pipes or fittings.
Improperly threaded couplings can lead to leaks, reduced pressure integrity, and overall system inefficiency. Therefore, adhering to industry standards such as ANSI/ASME B1.20.1 for NPT (National Pipe Thread) or ISO standards for metric threads is imperative for ensuring compatibility and performance.
Quality assurance processes play a pivotal role in producing reliable female threaded couplings. Manufacturers employ rigorous testing protocols, such as pressure testing and mechanical stress testing, to ascertain the coupling’s integrity and functionality under operational conditions. Testing for chemical resistance is also crucial, especially when couplings are destined for environments involving aggressive chemicals or high-pressure systems.
Installation expertise is another essential factor in maximizing the performance of female threaded couplings. Proper installation requires not only the right tools but also adherence to best practices, such as cleaning the threads to remove debris, applying a suitable thread sealant like PTFE tape or pipe dope, and ensuring that the coupling is not over-tightened to avoid damaging the threads or compromising the seal. Installers often must be well-versed in these techniques to ensure leak-proof and durable connections.
female threaded coupling
Maintenance is also a vital aspect of extending the lifespan of female threaded couplings and the systems they are part of. Regular inspections for signs of wear, corrosion, or damage can preempt potential system failures. Organizations should establish routine maintenance schedules and employ experts who can perform non-destructive testing and evaluations, making adjustments or replacements as required.
Beyond functionality, advancements in technology are enhancing the capabilities of female threaded couplings. Modern manufacturing techniques, such as CNC machining, allow for higher precision and customization of couplings to meet specific design and performance requirements. Additionally, surface treatments and coatings are being developed to enhance corrosion resistance and reduce friction, further optimizing coupling performance.
The adoption of female threaded couplings continues to grow as industries seek reliable and efficient methods of joining pipes. Their integration into automated and digitally monitored systems is becoming more common, wherein sensors can monitor coupling integrity, providing data for predictive maintenance and overall system optimization.
Selecting the right female threaded coupling for specific applications is crucial, involving assessing the operational environment, material compatibility, pressure and temperature requirements, and compliance with relevant industry standards. Consulting with experts who understand these variables can guide decision-makers in choosing the most suitable couplings for their needs, ensuring operational success and the longevity of their fluid transport systems.
In conclusion, female threaded couplings are more than just simple connectors; they are the backbone of numerous fluid-transport systems. Their reliability, coupled with technological advancements and adherence to stringent manufacturing and installation standards, secures their place as indispensable components in industries worldwide.