Finished casing coupling is a vital component in the oil and gas industry, functioning as the critical juncture where precision, expertise, and innovation converge. These elements not only enhance the efficacy of the coupling itself but also impact the entire drilling and extraction process.
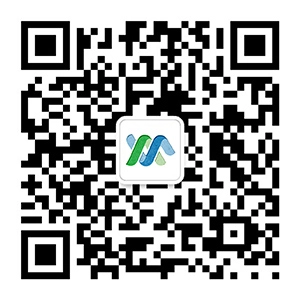
In the intricate world of well drilling, the coupling serves as a bridge connecting pipes securely. Its primary objective is to maintain the integrity of casing strings, which are vital for stabilizing the borehole and preventing contamination between rock formations. A high-quality finished casing coupling ensures this by being robust enough to handle the formidable pressures found deep within the earth, all while maintaining ease of installation.
Delving into the material composition, these couplings are often constructed from steel grades that have undergone meticulous testing for tensile strength and corrosion resistance. This choice of material ensures they can withstand harsh subterranean environments, enhancing their longevity and performance. Experts in metallurgy and engineering contribute significantly to developing these materials, ensuring they meet industry standards and beyond.

Precision machining is another cornerstone in manufacturing finished casing couplings. State-of-the-art CNC machines are employed to achieve the exact tolerances necessary for a seamless fit. This level of accuracy is non-negotiable, as even the slightest deviation can lead to equipment failure, posing immense financial and environmental risks. In this realm, technical expertise and quality assurance protocols are crucial, requiring seasoned professionals to oversee production.
finished casing coupling
The role of finished casing couplings extends beyond mere physical joining; they are pivotal in facilitating the transport of resources to the surface. As such, they are subject to rigorous testing regimes designed by industry experts. These tests mimic real-world stress conditions, ensuring that each coupling can perform reliably under extreme pressure variations and temperature changes. It is through these rigorous processes that manufacturers establish their authority as market leaders, setting benchmarks for safety and reliability.
Moreover, advancements in technology have ushered in enhancements such as anti-corrosion coatings and adaptive thread designs. These innovations are carefully researched and implemented by engineers and scientists dedicated to optimizing product performance. The continual refinement of finished casing couplings underscores the industry's commitment to safe, efficient, and sustainable operations.
In practice, the importance of finished casing couplings cannot be overstated. Operators in the field rely on them daily, trusting in their ability to secure joints without fail. The coupling's reliability is paramount, as any malfunction could lead to operational downtime or catastrophic well failure. This trust is built on a foundation of transparent manufacturing processes and the unwavering integrity of the materials used.
In conclusion, finished casing couplings epitomize the convergence of engineering prowess and industry know-how, combining innovation with steadfast reliability. As a linchpin in well integrity, their role extends far beyond mere connectivity. For professionals tasked with the critical job of resource extraction, they are a testament to human ingenuity and our ability to engineer solutions for some of nature's most formidable challenges.