Finished casing couplings are a critical component in the oil and gas industry, ensuring the integrity and safety of well operations. Expertise in manufacturing and the innovative engineering behind these couplings can dramatically affect the efficiency and success of drilling activities. This article delves into the unique aspects of finished casing couplings, drawing from professional expertise and authoritative insights from industry leaders, to highlight why they are indispensable in today's energy landscape.
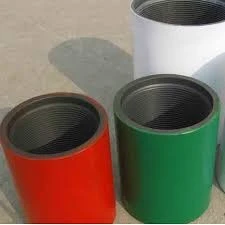
A finished casing coupling is essentially a short length of pipe used to connect two joints of casing. The casing itself is a large-diameter pipe inserted into a newly drilled section of wellbore, and the casing coupling secures these sections together. The robustness of these components ensures that the casing string can withstand the intense pressures and environments typically encountered in downhole applications.
In the realm of product expertise, the manufacturing process of finished casing couplings stands out as an area of specialized knowledge. Couplings are generally fabricated using high-grade steel and undergo stringent quality control measures, including hydrostatic testing and non-destructive evaluation, to ensure their durability and resistance to corrosion. Manufacturers often employ advanced threading techniques, such as API Round and BTC threads, which allow for a reliable seal and easy installation, reducing the risk of well failure.
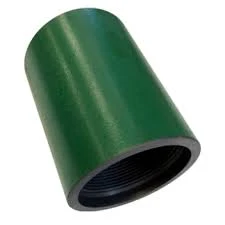
Industry authority is reflected in the standards and specifications that govern the production of finished casing couplings. Organizations such as the American Petroleum Institute (API) have set rigorous standards (e.g., API 5CT), which quality manufacturers adhere to. These standards ensure that the products operate safely and efficiently, maintaining structural integrity and preventing environmental hazards. Companies with ISO certification further demonstrate their commitment to quality management, enhancing their reputation in the marketplace.
Trustworthiness in a product, especially one as pivotal as a casing coupling, stems from both the credibility of the manufacturer and the proven performance of the coupling in the field. Leading manufacturers often provide detailed documentation and certifications, assuring buyers of the couplings' compliance with industry standards. Additionally, field testing and case studies serve as robust proof of the product's reliability, offering peace of mind to operators.
finished casing coupling
The real-world experiences of oil and gas professionals underscore the importance of finished casing couplings. Drilling engineers and field technicians often share anecdotal evidence that accentuates the role of high-quality couplings in reducing downtime and maintenance costs. Properly installed, these couplings ensure seamless operations, even in the most challenging geological formations and under extreme pressure and temperature conditions.
An understanding of the strategic importance and operation of finished casing couplings is also present. The selection of the appropriate coupling depends on various factors, including the specific conditions of the well, the material of the casing pipes, and the anticipated challenges during the lifecycle of the well. Customization and adaptability are key, with some manufacturers offering custom-designed couplings tailored to meet the unique needs of different drilling projects and geological formations.
The drive towards environmental sustainability in the oil and gas sector further accentuates the importance of reliable casing couplings. Ensuring that wells are sealed properly minimizes the risk of leaks and environmental contamination, aligning with global efforts to reduce ecological footprints. Thus, selecting quality finished casing couplings can be seen as both an operational requirement and an environmental imperative, supporting sustainable practices in exploration and production.
In conclusion, finished casing couplings are more than just simple connectors; they are vital for the safe and efficient extraction of oil and gas resources. Their design and manufacturing demand a high level of expertise and adherence to stringent standards, contributing to the product's authoritativeness and trustworthiness. As the industry evolves, so too will the technology and innovation behind these essential components, reinforcing their role in the ongoing development of global energy infrastructure.