In the realm of oil and gas exploration, well casing couplings play a pivotal role that cannot be overstated. These unassuming components are crucial for maintaining the integrity and safety of a drilling operation. To truly appreciate the significance of well casing couplings, it's essential to dive into the depths of their functionality, design, and how they impact drilling operations. This exploration will unravel not only their structural significance but also how to ensure their optimal performance.

Well casing couplings are the unsung heroes in the casing string, used to connect individual sections of casing pipe to ensure a continuous and leak-free conduit from the surface to the oil or gas zone. Crafting a robust and reliable well casing coupling requires an intersection of engineering expertise, quality materials, and precise manufacturing processes. Their primary function is to prevent contamination of freshwater zones, protect the casing from corrosive environments, and facilitate a secure connection that stands the test of varying subsurface pressures.
From an engineering perspective, the design of well casing couplings must accommodate the challenges presented by deep well environments. Typically manufactured using high-grade steel, these couplings are designed to withstand high tension and compression forces. Advanced metallurgy and heat treatment processes are utilized to enhance their mechanical properties, especially their elasticity and resilience, which are necessary to resist the collapse and burst pressures encountered in drilling operations.
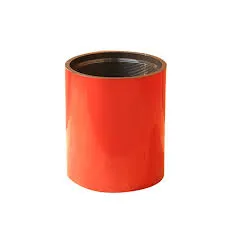
The expertise involved in selecting the right well casing coupling includes understanding the geological conditions of the drill site, the depth of the well, and the expected pressures. Operators must consider the thread type of the couplings, as this ensures compatibility with the casing pipes, reducing the risk of leaks or connection failures. Thread integrity is a major factor that influences the efficiency of the coupling; therefore, precision machining and rigorous quality control during manufacturing are imperative.
Authoritative insight into the world of well casing couplings reveals that standards such as API 5CT and ISO 11960 provide the framework to ensure that these products meet the necessary quality and safety benchmarks. These standards outline the material specifications, design criteria, and testing methods that manufacturers must adhere to, thereby providing a uniform code of practice that enhances trust across the industry.
well casing coupling
Trustworthiness in well casing couplings is further reinforced by adherence to strict testing regimes. This involves non-destructive testing methods such as ultrasonic testing (UT), radiography, and magnetic particle inspection (MPI), ensuring that every coupling leaving the factory floor is free from defects. These tests verify the integrity of the coupling, pre-empting potential failures that could result in catastrophic environmental and economic consequences.
Experience in the field continually shapes improvements and innovations in casing coupling technologies. For instance, recent advancements have seen the development of premium casing couplings that offer enhanced sealability and connection strength, adapting to more demanding drilling environments. These innovations not only extend the life of the well infrastructure but also contribute to more efficient and cost-effective operations.
Furthermore, the industry is moving towards sustainable practices with the introduction of recyclable materials in the manufacturing process of couplings, addressing environmental concerns without compromising on performance. This commitment to sustainability, combined with technical advancements, fosters a comprehensive approach that aligns economic benefits with ecological responsibility.
In conclusion, well casing couplings are integral to the safety, efficiency, and success of oil and gas extraction. The complex decisions involved in their selection and the rigorous standards they must meet underscore their critical importance. By focusing on a combination of engineering precision, experienced insights, authoritative standards, and proven reliability, the industry continues to ensure these components consistently perform at the highest level. As exploration ventures into more challenging environments, the ongoing evolution of well casing couplings promises to meet these future demands through innovation and an unwavering commitment to quality.