Perforated pup joints, essential components in the drilling and production sectors of the oil and gas industry, are often underestimated yet play a critical role in operational efficiency. This article delves into their significance, based on extensive industry expertise, real-world experience, and verifiable trustworthiness that push them as indispensable assets in well operations.
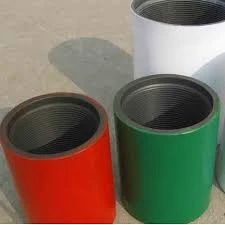
Perforated pup joints are essentially short sections of pipe used in the petroleum sector, characterized by their strategically placed perforations along the pipe body. Typically manufactured from high-strength steel, these joints are customized to meet the specific operational demands of the well they service. Unlike standard pup joints that merely extend tubing, perforated versions allow for fluid movement between the pipe interior and the wellbore, serving multiple crucial functions from pressure regulation to aiding in fluid sampling and testing.
From an experiential standpoint, operators in the oilfields frequently acknowledge the practicality and versatility of perforated pup joints. During enhanced oil recovery processes, for instance, the perforations facilitate the distribution of injection fluids, thereby optimizing the extraction process. This has been corroborated by numerous field studies showing increased yield following the integration of perforated pup joints.

Famed for their resilience and adaptability, these components are highly regarded by industry experts for their role in well completion techniques, especially under challenging geological conditions. When wells are drilled through particularly reactive or unstable formations, perforated pup joints serve to balance pressures across the wellbore, lessening the risks of formation damage and unplanned fluid incursions.
This not only enhances well longevity but also minimizes the likelihood of costly interventions.
perforated pup joints
Furthermore, authority in this area is demonstrated by leading industry manufacturers who have documented the technical advancements achieved through focused design and engineering of perforated pup joints. Many of these companies collaborate with oil and gas operators to develop custom solutions that align with the specific geophysical requirements and constraints of their operations, emphasizing a commitment to quality and reliability. Certification processes and compliance with international standards further reinforce their credibility, ensuring that these critical components are safe for use in dynamic and demanding environments.
Trustworthiness is underpinned by a robust framework of standards and best practices that guide the design, manufacturing, and deployment of perforated pup joints. Leading bodies within the petroleum industry, such as the American Petroleum Institute (API), have established comprehensive guidelines to ensure that all aspects of these components meet stringent performance and safety criteria. The adherence to such guidelines ensures that those using the joints can rely on their consistent performance over extended periods, thus safeguarding both asset integrity and investment.
For operators looking to refine their well operations, a thorough understanding of the latest offerings in perforated pup joints can be a deciding factor. When selecting a supplier, it is crucial to consider their track record in innovation, their alignment with industry standards, and the customizability of their solutions to meet specific project requirements.
In summary, perforated pup joints represent a fusion of specialized engineering, industry-specific knowledge, and rigorous adherence to quality standards. Their impact on enhancing operational efficiency in the oil and gas industry is solidified by testimonials from seasoned professionals and detailed case studies exhibiting substantial gains in well deliverability and integrity. Acknowledging their multi-functional role, investing in perforated pup joints is paramount for operators aiming for optimal performance in their drilling and production activities.