The oil and gas industry demands precision, reliability, and innovation, particularly when it comes to maintaining the integrity of pipelines. A component that continues to demonstrate its indispensable role in this context is the pipe bull plug. While often overshadowed by more high-profile equipment, the bull plug serves critical functions in various operations, ensuring safety and efficiency across the board. Understanding its utility, application, and the technical expertise required for its use can significantly enhance operational productivity.
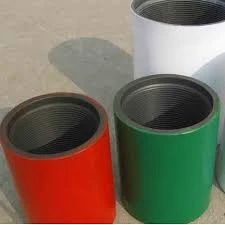
A pipe bull plug is a solid, cylindrical metal fitting used to seal the end of a pipe. Constructed typically from materials that ensure robustness, such as stainless steel or high-grade alloy, its primary purpose is to provide a secure and reliable seal in high-pressure environments. This component prevents leaks, maintains pressure, and safeguards the integrity of pipeline systems operating under extreme conditions. The expertise involved in selecting and implementing a bull plug cannot be understated, as even the smallest deficiency can lead to catastrophic system failures.
Expertise in the use of bull plugs comes not just from understanding their construction but also from implementing them in real-world scenarios. Field engineers, who often boast years of hands-on experience, meticulously select bull plugs according to specific industrial requirements – from the diameter of the piping to the anticipated pressure levels. This involves a deep understanding of the mechanical and chemical properties that influence the plug's performance, including resistance to corrosion, tensile strength, and temperature tolerance.
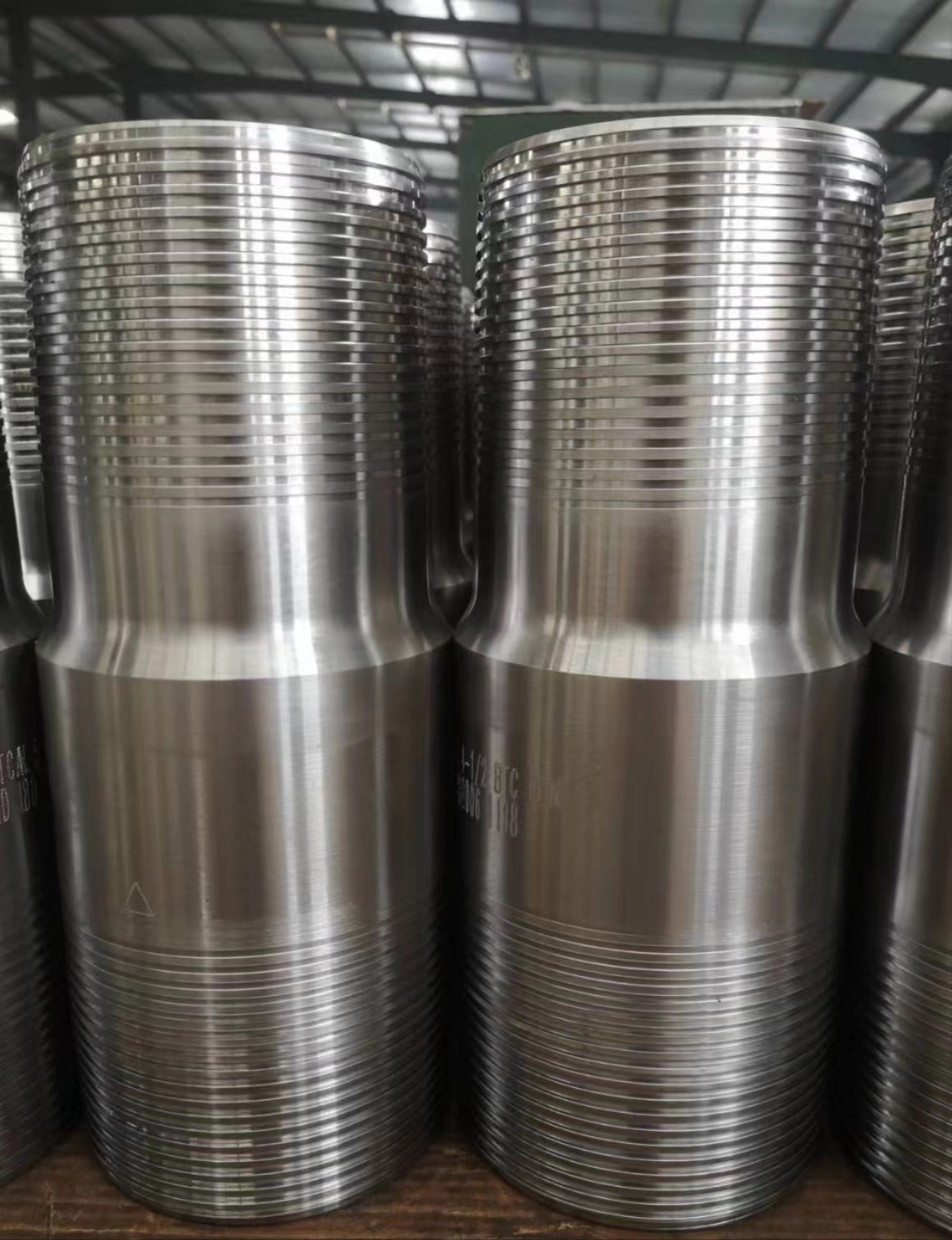
Moreover,
bull plugs are essential in temporary and permanent sealing of drilling strings. In drilling applications, they are typically deployed during transport or maintenance, essentially capping the pipe systems. This functionality highlights not just their mechanical importance, but also their role in safeguarding environmental standards. By preventing leaks or uncontrolled discharge of fluids or gases, bull plugs help maintain compliance with strict environmental regulations, thereby underlining their indispensable contribution to trustworthiness.
pipe bull plug
The utilization of pipe bull plugs in hydraulic fracturing further exemplifies their importance. In such high-stakes operations, where pressure management is crucial, the bull plug provides assurance against equipment failure. Their design must account for the highly specific conditions of hydraulic fracturing, and thus require precise manufacturing to ensure optimal performance. This highlights an extensive manufacturing expertise, where state-of-the-art technology and quality assurance converge to produce components that meet stringent standards.
Authoritativeness in the bull plug industry stems from manufacturers and suppliers who are recognized for their excellence in providing components that meet international standards. These companies invest heavily in research and development to produce bull plugs that not only meet but exceed industry expectations. With each deployment, the knowledge and feedback gained contribute to the advancement of product design and application strategies, reinforcing their status as industry leaders.
Trustworthiness is built through consistent track records of safety and performance. Organizations that rely on bull plugs do so because these components have consistently demonstrated their reliability under duress. Whether for small-scale applications or extensive pipeline projects, the bull plug's reputation for durability and effectiveness makes it a trusted component in the engineer's toolkit.
In conclusion, the pipe bull plug may initially seem a minor aspect of pipeline operations, but its importance is immense. Expertise, authoritativeness, and trust are all underscored by how this simple yet sophisticated component supports operations. For those engaged in industries where precision and safety are paramount, understanding and optimizing the use of pipe bull plugs is an investment in operational excellence. As global energy demands evolve and expand, the role of such components in maintaining safe, efficient systems will only continue to grow, solidifying their place in the industrial lexicon.