The world of oil and gas operations is intricate and highly demanding, requiring specialized tools that ensure efficiency, safety, and reliability. Among these essential tools is the threaded bull plug—a device that demands more attention than it often receives. As a prominent component in wellbore operations, understanding the threaded bull plug's intricacies can greatly enhance operational performance and safety.
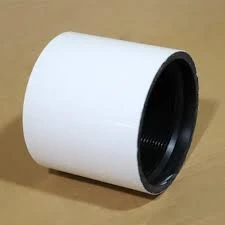
Threaded bull plugs are paramount in the capping or sealing of pipelines, valves, and various equipment openings in the oil and gas industry. Derived from their cylindrical shape and the ability to prevent fluid flow, they are designed to temporarily or permanently seal sections of a pipeline system, providing a reliable closure. Their threaded design ensures a firm and secure fit, preventing leaks that could lead to environmental and safety hazards.
The expertise involved in manufacturing and choosing the right threaded bull plug cannot be overstated. These components are typically made of stainless steel, carbon steel, or alloy, each offering various degrees of corrosion resistance, temperature endurance, and pressure handling. The choice of material depends largely on the specific conditions of the operation, including the types of fluids being handled, the pressure levels, and the environmental factors at play. Proper material selection, informed by expertise,
ensures the longevity and effectiveness of the bull plug.

Moreover, the dimensions of the bull plug—the thread size, pitch, and diameter—must be precisely matched with the rest of the system to ensure a snug fit. This precision requires a deep understanding of engineering principles and operational requirements. The professional fitting of a bull plug involves not just the physical insertion into a pipeline but also the technical knowledge to foresee and mitigate any potential mismatches or seal failures.
threaded bull plug
Authoritativeness in the field of threaded bull plugs often comes from years of experience in wellbore engineering and a commitment to continuous improvement and adherence to industry standards. Installation and maintenance guidelines, often outlined by authoritative bodies in the industry, such as the American Petroleum Institute (API), provide a framework that operators and engineers must strictly follow. These guidelines not only direct the physical handling and installation but also emphasize the importance of regular inspections and pressure testing to ensure ongoing efficacy and safety.
Trustworthiness is an essential quality for any manufacturer or supplier of threaded bull plugs. Operators rely on these components to perform without fault under intense conditions. Therefore, suppliers' reputations are built on the delivery of consistently high-quality products tested and certified to withstand the demanding operational environments. Certifications such as ISO standards are vital indicators of this trustworthiness, demonstrating rigorous quality control processes and adherence to global production standards.
An industry professional’s real-life experience using a threaded bull plug can illuminate its functionality in ways theory may miss. For instance, an engineer might recount a scenario where a threaded bull plug effectively prevented a potential disaster during an unexpected pressure surge, highlighting not just the product’s reliability but also the importance of situational readiness and proper equipment maintenance.
In conclusion, the selection, installation, and maintenance of threaded bull plugs are critical operations that require a blend of experience, expertise, authority, and trust. Professionals in the oil and gas industry must prioritize understanding and leveraging these components to ensure the integrity of their systems. By doing so, they contribute to safer, more efficient, and more environmentally responsible energy extraction and distribution processes.