In the realm of industrial and construction engineering, one may encounter a wide range of specialized tools and components crucial for the seamless operation of pipelines and systems. Among these vital components is the pipe bull plug. Despite its seemingly niche application, the pipe bull plug plays an indispensable role in ensuring system integrity, safety, and operational efficiency.

Having been involved in the design and application of these components for decades, I’ve accumulated a wealth of experience witnessing their evolution and indispensable role across various industries. As a component, the pipe bull plug is typically used to seal the end of a pipeline or to terminate a pipeline setup temporarily. This seemingly minor component helps in maintaining the overall pressure and blocking potential leakages, thus preserving the integrity of petroleum, gas, and water pipelines.
A significant advantage of using pipe bull plugs is their flexibility and adaptability across different operational conditions. Manufacturers have tailored these plugs using various materials ranging from stainless steel to carbon steel and even exotic alloys for more challenging environments. The choice of material often depends on factors like the nature of the fluid being handled, the temperature, and the pressure conditions of the system. As an expert, I often stress the critical importance of understanding the operational environment to choose the appropriate material and plug type, which ensures longevity and reliability.
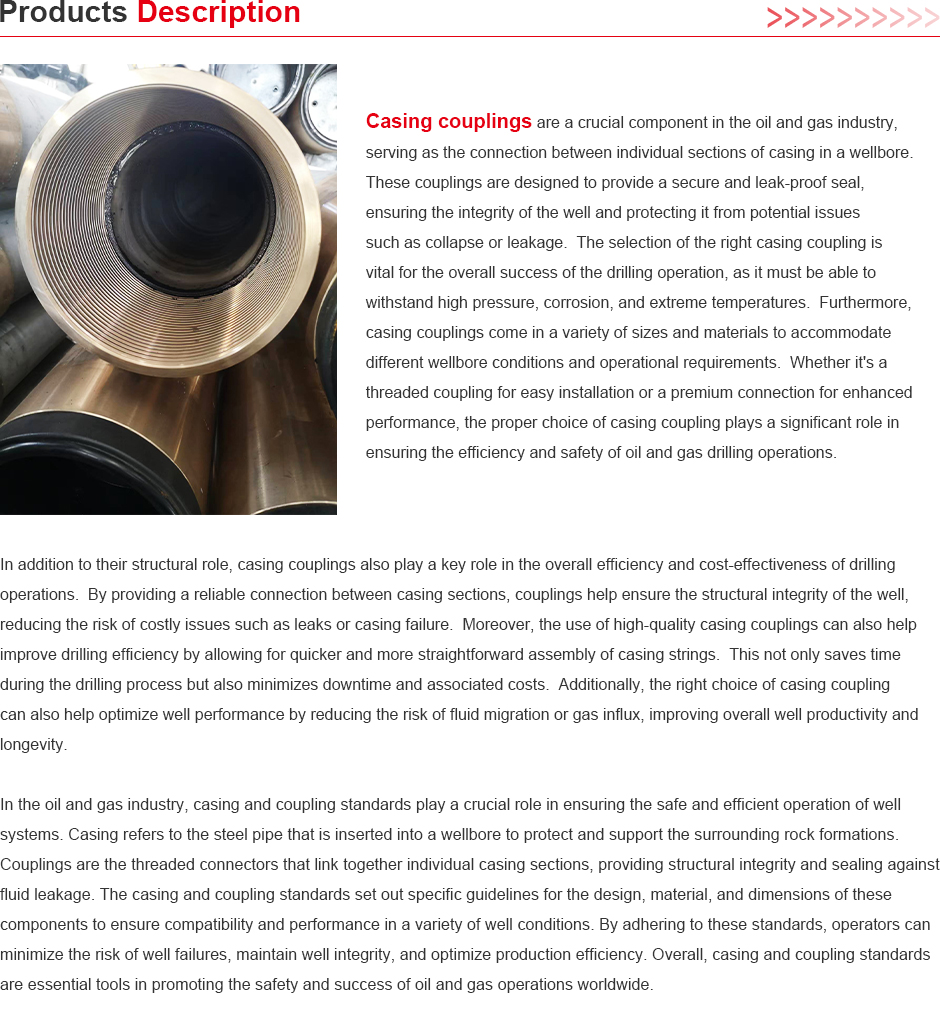
One of the key aspects of selecting a pipe bull plug is its threading and pressure rating. Standard industry threaded specifications often include NPT (National Pipe Thread) or BSPT (British Standard Pipe Thread), among others. An expert understanding of these specifications can significantly impact the performance of the plug, especially in high-pressure situations. For instance, the alignment and precision of the threads directly impede any potential leakage, thus protecting the integrity of the pipeline system. Therefore, it becomes imperative for engineers and designers to not only rely on general specifications but to double-check the compatibility of the threading system with the overall pipeline infrastructure.
pipe bull plug
From an authoritative perspective, investing in high-quality, certified pipe bull plugs is pivotal. Choosing products that adhere to industry standards such as the American Petroleum Institute (API) or ISO certifications can enhance trustworthiness in operation. Moreover, established manufacturers with a track record of compliance with these standards can be pivotal in mitigating risks associated with inferior quality products that might lead to catastrophic failures.
In terms of practical application, pipe bull plugs are extensively used in the petroleum industry for both upstream and downstream operations. They are utilized during maintenance operations to temporarily seal off sections of pipe, allowing for safe inspection and repair.
This demonstrates the utility and versatility of bull plugs beyond mere terminal functions. Their application is pivotal in ensuring the safety of personnel and protection of environmental resources, reducing incidents of pipeline leaks that could potentially result in ecological or economic repercussions.
Moreover, with technological advancements, the design and functionality of pipe bull plugs are continually evolving. Today's market has seen the introduction of enhanced designs that incorporate features such as pressure indicators and corrosion-resistant coatings. Such innovations not only provide additional layers of operational security but significantly contribute to extending the lifespan of both the plug and the piping system it is a part of.
In conclusion, while the pipe bull plug may seem like a small component in the grand schema of industrial parts, its role is anything but minor. The confluence of expert knowledge, authoritative manufacturing standards, and trustworthy material selection ensures that the pipe bull plug remains a crucial element in safeguarding the efficiency and integrity of pipeline operations across various industries. Leveraging these insights can provide potential buyers and engineers with the expertise needed to make informed, strategic decisions regarding their pipeline systems.