Pipe mills play a pivotal role in the manufacturing and construction industries by producing high-quality pipes essential for infrastructure, oil and gas transportation, water conveyance, and more. As the demand for robust and efficient piping solutions grows, understanding the intricacies of pipe mills becomes crucial for businesses looking to make informed decisions.

The process of pipe milling involves multiple stages, each contributing to the final product's strength, durability, and functionality. Raw materials, typically steel or aluminum, are meticulously sourced to ensure they meet stringent industry standards. The pipe mill process begins with uncoiling large sheets of metal, which are then leveled to ensure uniformity. This step is critical for maintaining the integrity and dimensional accuracy of the pipes.
Following this, the metal sheets undergo a forming process where they are shaped into a cylindrical form. Innovative techniques such as the high-frequency induction (HFI) welding are employed to join the edges seamlessly. This method ensures the weld is as robust as the parent material, offering unparalleled reliability in various applications, from high-pressure environments to corrosive substances.
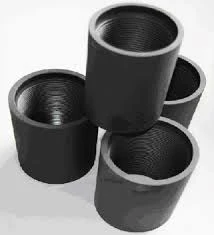
Expertise in metallurgy is vital at this stage, as different metal compositions can affect weldability and the final product's properties. Experienced metallurgists in pipe mills work diligently to assess and adjust the material composition to achieve the desired characteristics, such as resistance to corrosion, ease of welding, and tensile strength.
Pipe mills are also equipped with advanced testing facilities to maintain the highest quality standards and ensure trustworthiness. Non-destructive testing (NDT) methods such as ultrasonic testing, radiography, and hydrostatic testing are commonplace. These tests identify internal defects or inconsistencies, ensuring only pipes that meet the rigorous requirements make it to market.
pipe mill
Beyond production, the expertise of pipe mills extends to personalization and customization.
Clients often require pipes with specific dimensions, coatings, or threading. Modern pipe mills leverage cutting-edge technology to cater to these needs, offering a diverse array of coatings that enhance longevity and performance under harsh conditions, such as polyethylene and fusion-bonded epoxy coatings.
In terms of environmental consciousness, leading pipe mills integrate sustainable practices within their production lines. Energy-efficient machinery, recycling programs, and waste reduction initiatives demonstrate a commitment to sustainability, addressing global concerns about industrial impact on the environment.
The authoritativeness of a pipe mill is often reflected in its certifications. ISO certifications, adherence to ASTM standards, API specifications, and other industry-recognized credentials signify a company's dedication to quality and safety. These certifications provide customers with confidence, knowing they are sourcing from compliant and reputable suppliers.
To remain competitive, pipe mills continually invest in research and development. Innovative breakthroughs such as smart sensors that provide real-time monitoring of pipe integrity or advancements in anti-corrosion technology keep pipe mills at the forefront of the industry, offering clients state-of-the-art solutions.
In summary, pipe mills are the backbone of many industries, providing the conduit through which vital resources flow. Their role in supporting infrastructure, enabling energy production, and facilitating water distribution cannot be understated. By emphasizing expertise, quality assurance, environmental responsibility, and cutting-edge innovation, pipe mills establish themselves as authoritative and trustworthy players in the global market.