In the world of oil and gas production, the role of a seating nipple in tubing cannot be overstated. This small yet pivotal component offers an array of advantages to enhance the efficiency and safety of well operations. Drawing from extensive industry experience and technical expertise, this article delves into the crucial aspects of seating nipples, solidifying its position as an authoritative resource for engineers, operators, and procurement professionals alike.
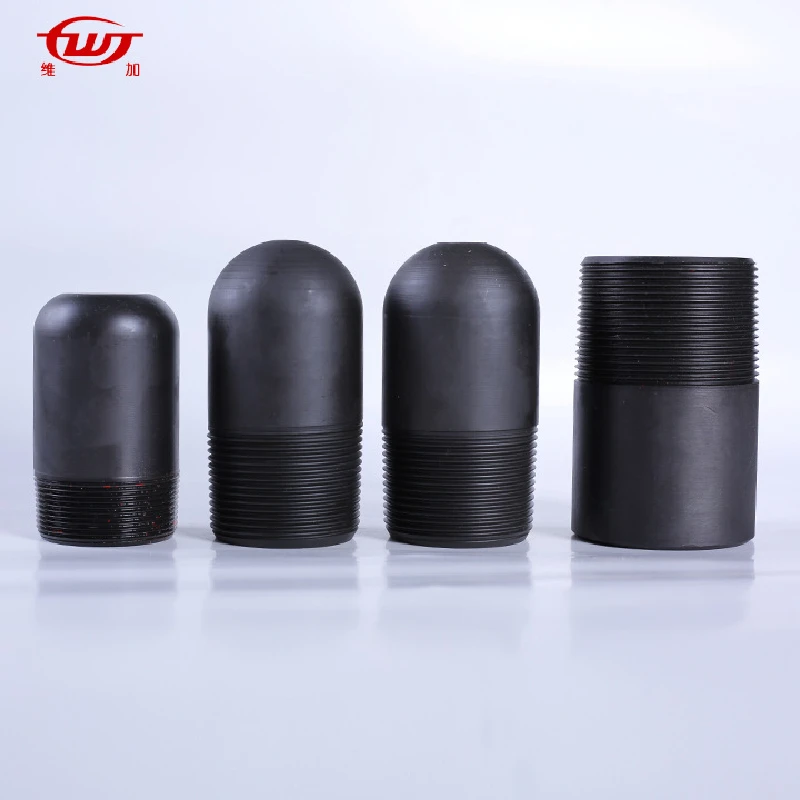
Seating nipples, embedded within the well tubing string, serve as the designated point where downhole tools, such as plugs or flow regulators, latch onto. Their design ensures that these tools remain securely seated, providing a reliable seal that can be critical in various operational stages—whether maintaining pressure, isolating zones, or managing the flow of fluids. Given their integral role, seating nipples are crafted from high-quality materials that withstand the harsh conditions of the downhole environment, including extreme pressures and erosive fluids.
From a technical standpoint, seating nipples are designed with precision and accuracy that aligns with stringent industry standards. Their inner profiles are tailored to marry perfectly with the complementary tool components. Usually made from robust alloys, advanced manufacturing processes ensure that these nipples maintain structural integrity over extended periods, even under significant mechanical stress.
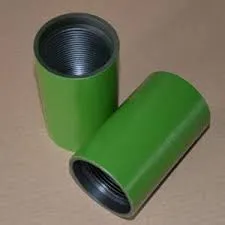
Experience in diverse field operations reveals that the proper selection and deployment of seating nipples bolster operational efficiency immensely. Engineers often witness marked improvements in well performance when these components are integrated correctly. The assurance of tool stability reduces the risk of premature equipment failure and mitigates costly production downtime—a critical advantage in the highly competitive energy sector.
Expertise gained over decades has shown that when choosing a seating nipple, several factors warrant meticulous consideration. Compatibility with existing tubing threads, pressure ratings, temperature tolerances, and material composition all play pivotal roles. In-depth analysis and simulation of well conditions can guide the customization of nipples to fit specific operational needs, offering bespoke solutions to complex challenges.
seating nipple in tubing
Beyond practicality, the seating nipple's contribution extends to enhancing the trustworthiness of well operations. As a function-centric piece of equipment, its presence assures stakeholders of robust operational reliability. When stakeholders recognize that critical components like the seating nipple are optimized and tailored for their specific requirements, confidence in system integrity increases.
Moreover, innovation continues to fuel the evolution of seating nipple technology. Recent advancements include the development of corrosion-resistant surfaces and coatings, mitigating risks of damage over prolonged exposure to harsh substances. Companies deploying such cutting-edge solutions can lay claim to heightened environmental responsibility and cost-effectiveness, as maintenance intervals are naturally extended.
Suppliers of seating nipples also play a critical role in ensuring product quality and reliability. Working with reputable manufacturers who prioritize rigorous testing protocols, including fatigue resistance and sealing efficiency assessments, is essential. Certifications from recognized industry bodies further attest to compliance with international standards, fostering trust and confidence in product offerings.
Leveraging digital solutions, such as comprehensive product databases and AI-driven simulations, equips professionals with invaluable insights, empowering informed decision-making. Online platforms enable easy comparison of product specifications, performance reviews, and field data, fostering a more transparent selection process.
In conclusion, the significance of seating nipples in tubing speaks to more than just their mechanical function within a well system. It embodies a confluence of experience, technical mastery, authority in production processes, and unwavering trust. Such components are not merely parts of a system; they are enablers of progress, ensuring the complex orchestration of oil and gas extraction is carried out with precision and reliability. As the industry continues to evolve, so too will the innovations surrounding these essential tools, driving the next frontier of energy exploration and production.