Seating nipples in tubing play a crucial role in the functionality and efficiency of oil and gas well completions. These critical components ensure that downhole tools can be reliably set within the wellbore, optimizing resource extraction while avoiding costly operational mishaps. Below we delve into the essentials of seating nipples, their expert design aspects, and why their reliability is pivotal for successful oil and gas operations.
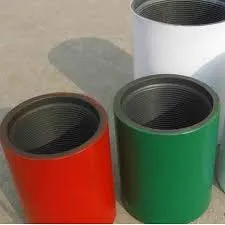
Seating nipples, sometimes referred to as profile nipples, are short sections of the tubing string designed with a specific internal profile to accept a particular type of plug or flow control device. They are often placed at strategic locations within the tubing string to provide control over the production process. Typically made from high-strength steel or corrosion-resistant alloys, these devices must withstand extreme downhole conditions such as high pressure and corrosive environments.
Boasting a solid reputation for precision, seating nipples ensure that production tools, such as flow control devices and safety valves, can be securely anchored within the tubing, enabling seamless control over fluid flow. An expertly designed seating nipple provides a reliable seat for tools that can isolate specific sections of the well, regulate flow rate, or even serve as a component in a larger safety mechanism to shut down production in emergency situations.
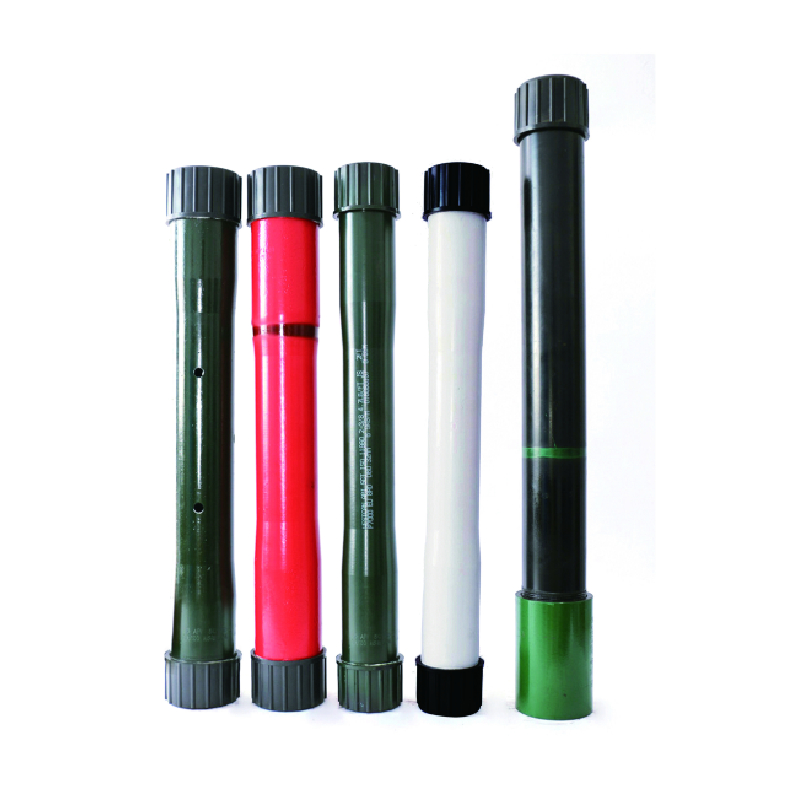
A key aspect of seating nipple design is the precision of their internal profiles, which must align perfectly with the corresponding profiles of the devices they host. Misalignment can lead to incomplete setting or failures, potentially causing expensive downtime and repairs. Thus, engineers use advanced machining techniques to ensure each nipple meets exacting industry standards. This precision guarantees a high success rate for seating and retrieval operations, thus maximizing the productive lifespan of the well and optimizing resource recovery.
seating nipple in tubing
Another aspect of seating nipple functionality is their compatibility with retrievable plugs and chokes. These components often need to be inserted and removed multiple times over the lifespan of a well. Therefore, seating nipples must be durable and resistant to wear, maintaining their integrity despite repeated use. High-quality materials and robust engineering designs ensure the seating nipples withstand the mechanical stresses associated with repeated insertions and removals, all while maintaining a secure and reliable seal.
Seating nipples also play a role in well integrity management. By allowing for the installation of downhole barriers, they help prevent the uncontrolled release of hydrocarbons, ensuring that production activity complies with regulatory standards designed to protect the environment and personnel. In emergency scenarios, quickly deployable plugs can be seated to halt production, safeguarding the well from damage.
From a production strategy perspective, choosing the right seating nipple requires a balance between function, material selection, and compatibility with downhole tools. Consultation with experienced well completion engineers is critical to select a nipple profile that suits the specific requirements of a given well operation.
In conclusion, seating nipples in tubing are indispensable components for any efficient oil and gas production strategy. They offer unique value through their precision, durability, and adaptability. With the ongoing demand for optimizing well productivity and maintaining safety, seating nipples will continue to be crucial in maximizing the exploitation of hydrocarbon resources. Their expert design and reliable performance build trust in their use, making them a cornerstone in modern well completion technologies.