Seating nipples in tubing play a crucial role in the oil and gas industry, providing a reliable means of establishing a sealing point within a wellbore to facilitate various production processes. These small but vital components are the backbone of much larger operational capabilities. Understanding their importance and functionality not only enhances operational efficiency but also ensures the longevity and safety of equipment. As someone who has spent decades working with these components and seeing their effect on large-scale projects, I am excited to share my insights.
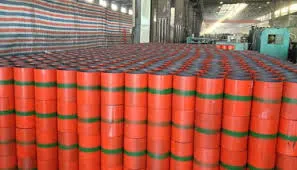
Seating nipples serve as seating points for various downhole tools, such as plugs and chokes, allowing operators to isolate sections of a well for maintenance, testing, or production. Their ability to maintain integrity under extreme pressures and temperatures underscores their essential function in the industry. Typically made of high-grade steel alloys, seating nipples are precision-engineered to withstand the harsh conditions found deep underground.
Experience in deploying these components has taught me that the choice of seating nipples can significantly affect operational outcomes. Their selection should be informed by a keen understanding of the wellbore environment and the specific project requirements. For instance, the appropriate size and type of nipple are determined by factors such as the diameter of the wellbore, the nature of the fluids being extracted, and the operational pressures expected.

When it comes to expertise in the installation process, precision is of the utmost importance. Misalignment or incorrect installation can lead to inefficient sealing, which may cause production delays or even catastrophic failures. It is imperative to have a skilled team equipped with the right tools and knowledge to carry out this task. A successful installation not only requires mechanical precision but also a deep understanding of the well's geological profile to predict and mitigate potential problems.
seating nipple in tubing
The authority of seating nipples within tubing systems is further established through rigorous testing and compliance with industry standards. Reputable manufacturers adhere to stringent quality control measures, ensuring each component meets the required specifications for pressure resistance, temperature tolerance, and chemical compatibility. Certifications by recognized bodies add an additional layer of assurance, confirming the product’s capability to perform reliably in demanding environments.
Trustworthiness is not simply a function of the components themselves but also of the teams involved in their deployment and maintenance. Transparency in communication, continuous education, and adherence to safety protocols form the foundation of a trustworthy operation. Building trust with stakeholders involves not only correctly installing and maintaining seating nipples but also openly discussing potential issues, solutions, and taking proactive measures to address them.
Ultimately,
the use of seating nipples in tubing represents a confluence of technology, expertise, and strategic planning. Companies looking to optimize their production processes must consider these elements carefully. Investing in high-quality seating nipples, alongside ensuring that teams are fully trained and aware of the latest industry developments, can translate to significant production efficiencies and cost savings.
In conclusion, the integration of seating nipples in tubing systems demands a multidisciplinary approach that leverages real-world experience, technical expertise, authoritative product standards, and a commitment to transparency and reliability. With these pillars in place, the operational efficiency and safety of oil and gas extraction can be significantly enhanced, paving the way for more sustainable and profitable ventures.