The oil and gas industry operates with a myriad of intricate components, but at the heart of any drilling operation lies the critical infrastructure of tubing and casing. Mastery over these components is paramount for ensuring efficient resource extraction, safety, and operational longevity.
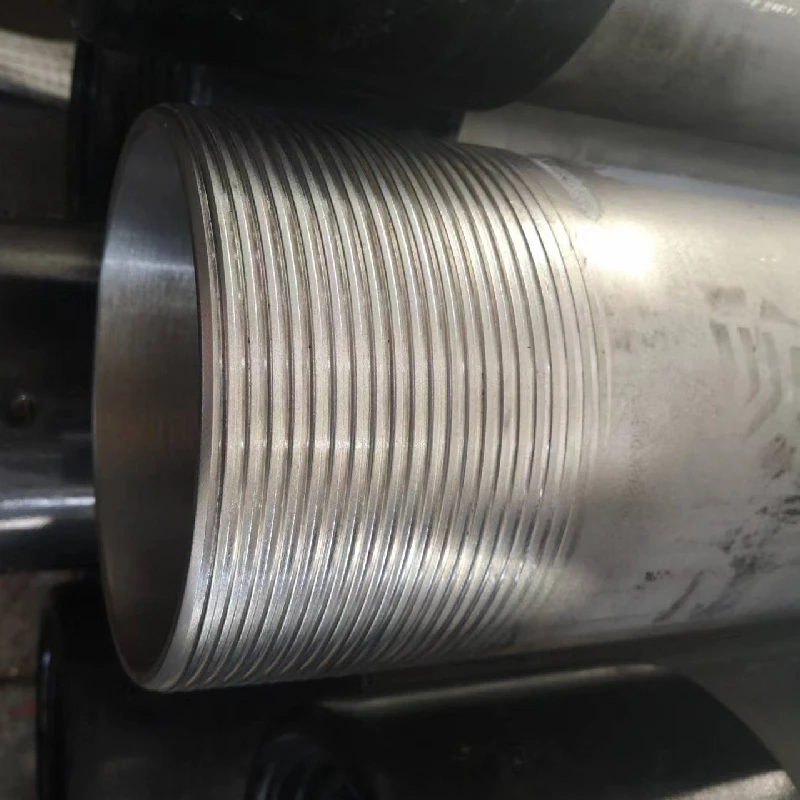
Tubing and casing play distinct yet intertwined roles in the lifecycle of a well. Casing is the robust, larger-diameter pipe that is cemented in place within the drilled wellbore. Its primary functions include stabilizing the wellbore, isolating different subsurface pressure zones, preventing contamination of freshwater aquifers, and providing a conduit for drilling fluids. Selecting the right type of casing is pivotal, depending on the geology, depth, and pressure characteristics of the well. This requires expertise in understanding and predicting subsurface conditions, which can vary significantly even within the same field.
Tubing, on the other hand, is the conduit through which oil and gas are brought to the surface once the well is completed. Unlike casing, tubing is subject to continuous replacement and is usually smaller in diameter. The material selection for tubing is critical as it must withstand the produced fluids' corrosive properties and the pressures involved in hydrocarbon extraction. The grading and thickness of the tubing are selected based on a detailed analysis of the reservoir pressures, temperatures, and expected lifespan of the well, showcasing the interplay between engineering acumen and real-world experience.

A practical experience shared by industry experts reveals that missteps in the design or installation of tubing and casing can lead to catastrophic failures. These include blowouts, environmental contamination, and costly well workovers or abandonments. For instance, a case study conducted on a well in the North Sea highlighted how inadequate casing lead to a slow seepage of hydrocarbons that went undetected until it escalated into a significant environmental challenge. This emphasizes the trustworthiness of investing in quality products and services, and also the importance of precise engineering and adherence to safety protocols.
tubing and casing
As technologies advance, the tubing and casing sector evolves with innovations focused on enhancing performance and extending the lifecycle of wells. Materials with better corrosion resistance, such as advanced alloys, and smart tubular technologies that provide real-time data on subsurface conditions are increasingly being adopted. Industry leaders, through their authoritative research, have shown that leveraging these technologies can lead to a 15-20% reduction in operational costs and a significant decrease in non-productive time.
Furthermore, the expertise of supply chain management in tubing and casing cannot be overlooked. Ensuring that quality standards, such as those set by the American Petroleum Institute (API), are not just met but exceeded, forms the backbone of a reliable wellbore structure. These standards encompass not only the physical aspects of the tubing and casing but also the processes related to manufacturing and handling. Viable solutions are curated through an extensive understanding of both the theoretical underpinnings and practical implications, making companies that adhere to these standards a trustworthy choice.
In conclusion, tubing and casing are not mere components of the well structure; they are critical determinants of a well's success, safety, and economic viability. Their selection and implementation require a deep reservoir of experience, technical expertise, and adherence to authoritative standards to ensure trustworthiness. The vigilant oversight of these aspects exemplifies the industry’s commitment to optimizing resource extraction while prioritizing safety and environmental stewardship. Thus, strategic decisions in tubing and casing are investments not only in the immediate operation but in the sustainable future of the oil and gas industry.