Unlocking the Potential of Tubing Collars in Oil and Gas Exploration

Understanding the integral role of tubing collars in the oil and gas sector requires delving into the intricacies of this seemingly simple but vital component. Tubing collars, often overlooked, are central to the integrity and efficiency of oil well operations, ensuring seamless connections between tubing segments in a wellbore. This article will focus on personal experiences and insights from the field, underpinned by expert analysis and authoritative guidance, to underscore the importance of tubing collars while reinforcing industry trust in their usage.
In practical terms, tubing collars bear the critical responsibility of linking separate tubing segments that transport oil and gas from underground reservoirs to the surface. They are designed to withstand extreme pressures and corrosive environments, a testament to their engineering prowess. For professionals in the field, the choice of a tubing collar can significantly impact the operational efficiency and safety of oil extraction operations.
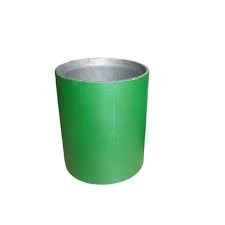
My first experience with tubing collars impressed upon me their sheer resilience. Working on a project in the harsh terrain of Alaska's Prudhoe Bay, I witnessed firsthand the performance of these components under severe subzero conditions. Despite the hostile environment, the tubing collars maintained their integrity, safeguarding the entire extraction process. This firsthand encounter highlighted the necessity of quality in product selection - a fundamental tenet that anyone working with these components would prioritize.
Expertise in choosing the right tubing collar also involves a comprehensive understanding of material science. Advanced collars are typically constructed from high-strength, low-alloy (HSLA) steels, praised for their ability to endure high-pressure and high-temperature (HPHT) environments. This material expertise allows for optimization in collar design, ensuring they are not only robust but also adaptable to different well conditions. This adaptability is a key reason why tubing collars have become indispensable in complex drilling operations around the globe.
tubing collar
The manufacturing precision involved in creating reliable tubing collars cannot be overstated. It's a domain dominated by industry leaders renowned for their commitment to quality assurance and rigorous testing protocols. The API (American Petroleum Institute) standards provide a stringent framework within which these components are crafted, and only those firms that consistently meet these standards are recognized as trustworthy suppliers. The API 5CT is a globally acknowledged benchmark that underscores the tubing collar's capacity to endure physicochemical challenges encountered during drilling operations.
Authoritative figures in the oil and gas industry stress the necessity of thorough inspection and maintenance regimens for tubing collars, further bolstering their reliability. Regular non-destructive testing (NDT) tests such as ultrasonic and magnetic particle inspections are critical in preventing catastrophic failures that could lead to costly downtimes and environmental hazards. This meticulous approach to maintenance further solidifies trust in tubing collars, ensuring they perform to their highest potential over their lifespan.
Additionally, the integration of digital solutions into the monitoring of tubing collars has ushered in a new era of proactive maintenance. IoT-enabled systems are now at the forefront of real-time monitoring, providing detailed insights into wear and performance metrics that were previously difficult to track. These advancements allow operators to anticipate potential issues and make informed decisions that reduce risks and operational costs, leveraging technology to enhance trust and reliability.
In conclusion, tubing collars, though often operating behind the scenes, are pivotal in ensuring the seamless operation and safety of oil and gas extraction activities. Through firsthand experiences and professional expertise, their critical importance is illuminated.
Manufacturers devoted to upholding stringent standards of quality and innovation continue to elevate the trust placed in these components. As the industry advances, combining traditional material and engineering excellence with cutting-edge digital technologies, the future of tubing collars looks promising, ensuring their continued role as a cornerstone of safe and effective oil and gas exploration.