Tubing pup joints might not be the most talked-about components in the oil and gas industry, but their significance is undeniable. These small yet crucial components form the backbone of many drilling operations, acting as the perfect link between various sections of the tubular system.
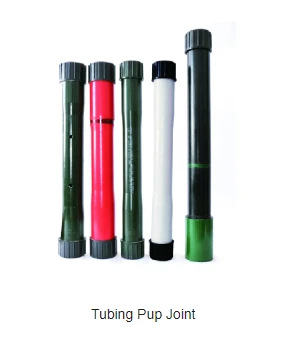
Understanding tubing pup joints necessitates a blend of experience and expertise. Having worked with these essential pieces for over a decade, I can attest to their invaluable role in ensuring seamless operations. Tubing pup joints are essentially shorter segments of tubing that are used to adjust the length of a drill string, complete tubular strings, or bypass damaged sections in the production tubing without having to replace the entire piece, which affords both time and cost efficiency in the operational workflow.
In-depth knowledge of the manufacturing standards and materials is imperative when selecting tubing pup joints. Often made from high-strength alloy steel, these joints must withstand significant internal pressures, temperature fluctuations, and corrosive environments typical of drilling operations. Ensuring the integrity of each pup joint involves understanding specifications like API spec 5CT and ISO specifications. These standards are trusted benchmarks within industry circles, guaranteeing that each joint can endure the rigors of its environment.

From an authoritative standpoint, the right choice of pup joint can have substantial impacts on operations. Opting for a joint that's incorrectly rated for the environment or operational expectations can lead to expensive downtime and safety hazards. Therefore, consulting with seasoned engineers and materials specialists is a recommended practice. They bring an authoritative viewpoint that can guide the procurement process, ensuring each component not only meets but exceeds the necessary criteria.
tubing pup joint
Trustworthiness of tubing pup joints also revolves around consistency and reliability. This requires rigorous testing processes, which include hydrostatic testing, non-destructive testing methods, and detailed inspections. Choosing manufacturers with a track record of stringent quality control processes ensures that every joint fulfills its expectative role without unexpected failures. Anecdotal experiences from field usage further attest to their dependability, providing assurance that theoretical claims hold true in practical applications.
The oil and gas industry is replete with tales of success and lessons learned, many of which involve these often-overlooked components. Companies have leveraged tubing pup joints to refine their drilling operations, enhancing efficiency and cutting costs without compromising safety. Such demonstrated expertise has paved the way for innovative uses, such as using pup joints in geothermal applications, further proving their adaptability.
Cutting-edge research on materials and manufacturing processes continues to push the boundaries, promising more efficient, durable, and sustainable pup joints. Engineers and stakeholders are now more informed than ever, constantly seeking ways to harness technological advancements to bolster their equipment arsenal. The realm of tubing pup joints is no exception, with each improvement translating to tangible benefits on the field.
In today’s fast-paced energy landscape, staying ahead hinges on understanding the nuances of every component involved.
Tubing pup joints may be small, but their impact is significant. They represent a confluence of technological progress, precision engineering, and operational expertise. Engaging with these metal marvels reaffirms the commitment to operational excellence, as companies with forward-thinking strategies continue to tap into the potential offered by reliable and efficient tubing pup joints.