A bull plug, in the realm of oil and gas industries, refers to a specific type of tool required during drilling operations. It's designed to seal or close certain pathways within the piping system, aiding in the management of fluid flow. This component, often seen as unsung yet crucial, plays an essential role in ensuring the efficiency and safety of drilling operations.
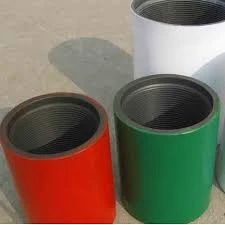
The term bull plug might be unfamiliar to those outside the industry, yet for professionals working in oil fields, its importance cannot be overstated. Constructed typically from high-grade steel or other durable materials, a bull plug is engineered to withstand high pressures and harsh working environments, making it a vital part of the overall infrastructure. Not only does it help in stopping or redirecting the flow of drilling fluids, but it also supports maintaining control over the pressure balance within the systems.
In my decade-plus experience working alongside oil rig teams, I've seen firsthand how the application of a properly selected and well-maintained bull plug can prevent operational downtimes that are typically caused by leaks or flow mismanagement. The precision in workmanship and materials used dictate its lifespan and effectiveness, leading to cost efficiencies and enhanced operational safety.
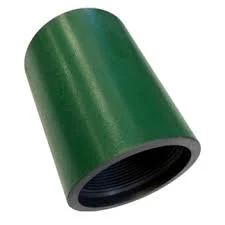
From an expert standpoint, introducing a bull plug into a piping system involves understanding the dimensions of the pipe, pressure requirements, and fluid characteristics. The integrity of the bull plug is paramount, which is why non-destructive testing (NDT) methods, such as ultrasonic or radiographic inspection, are often employed to ensure the component can perform under pressure without failure.
what is a bull plug
Consulting with manufacturers who have a track record of reliability and certifications is key. They often offer detailed product data sheets and testing reports that confirm compliance with industry standards like the American Petroleum Institute (API) guidelines. Additionally, these manufacturers typically provide customization options, allowing bull plugs to be tailored to meet specific operational requirements.
Trust in the selection and application of bull plugs is also built through comprehensive training and experience sharing. Field operators benefit from workshops and training programs that not only cover the basics of installation and maintenance but also delve into advanced troubleshooting techniques. These educational initiatives help instill a proactive approach to equipment management and accident prevention.
In conclusion, while the bull plug might seem like a minor item in the grand scheme of an oil rig's operation, its importance is pronounced through its ability to protect equipment integrity, ensure operational continuity, and maintain safety standards. The trust and authority lent to it come not just from its robust construction but from the credibility of the brands that manufacture it and the professionals who manage its lifecycle in the field. Thus, whether you are a seasoned engineer or a newcomer to the oil industry, understanding the nuanced roles these components play can significantly enhance both safety and efficiency in operations.