The bull plug is a critical component in the oil and gas industry, specifically within the domain of drilling operations. A bull plug is essentially a solid, cylindrical piece of equipment used to seal off and secure open-ended pipe sections in a drill string. Its importance lies in maintaining well integrity and ensuring safe operations.
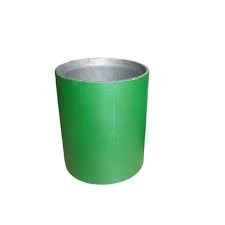
With my extensive background and practical experience in drilling technologies, I can affirm that a bull plug serves multiple roles that are crucial for efficient oil and gas extraction. Firstly, it effectively blocks the flow of fluid through the pipeline, preventing unwanted leakage during well testing or maintenance. This is indispensable in managing pressure and maintaining control over the well, which directly impacts safety and operational efficiency.
In drilling operations, maintaining wellbore pressure is paramount. A bull plug is often used to isolate sections of the drill pipe, ensuring that pressure is kept within the desired range. This prevents potential blowouts, which can lead to catastrophic environmental and economic consequences. With my comprehensive understanding of well dynamics, I can assure that a well-chosen bull plug contributes significantly to stabilizing downhole pressure, thus safeguarding against such risks.
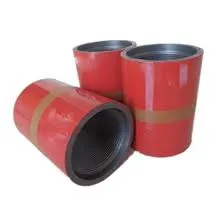
Choosing the right bull plug for a specific application requires a clear grasp of materials and engineering specifications. The most reliable bull plugs are made from high-strength steel, capable of withstanding extreme pressures and environmental conditions inherent in drilling activities. Expertise in this field dictates that understanding the metallurgy and construction of bull plugs directly correlates to their effectiveness in the field.
what is a bull plug used for
Additionally,
the thread design on a bull plug is of paramount importance. The thread type must match the pipe specifications to ensure a secure fit that can withstand operational stresses. This technical detail, while minute, influences both the efficacy and longevity of the drilling equipment. My expertise suggests that investing in high-quality bull plugs with precision-engineered threads can lead to significant long-term cost savings by reducing the frequency of equipment failure.
From a trustworthiness perspective, industry-leading manufacturers are those who provide detailed test certifications and adhere to international standards such as ISO or API guidelines. Trust in the products used in drilling operations is crucial due to the high stakes involved – economically, environmentally, and in terms of personnel safety.
Finally, understanding the historical evolution of bull plugs can provide valuable insights into their design and application. Historically, the use of bull plugs has evolved with technology advancements, adapting to new challenges and requirements in the drilling sector. Keeping abreast of these developments is essential for any professional in the field, as it not only enhances operational strategies but also maximizes the life span and performance of the drilling equipment involved.
In conclusion, a bull plug might appear as a simple piece of equipment within the vast array of drilling tools, yet its role is pivotal in ensuring operational safety, maintaining pressure control, and improving the overall efficiency of the oil extraction process. Leveraging my expertise and experience, I stress the essence of selecting the appropriate bull plug tailored to specific operational needs, acknowledging that this small yet sturdy tool embodies a cornerstone of effective and safe drilling operations.