In the realm of downhole tools and oilfield jargon, the term bull plug stands out as a critical component for maintaining well integrity and flow control. Understanding the characteristics, applications, and benefits of a bull plug can significantly impact how the oil and gas industry conducts its operations. Here's an in-depth exploration of bull plugs focusing on the expertise and practical experiences that shape their utility.

A bull plug is a type of pipe fitting used primarily in oilfield applications to terminate or seal the end of a piping system. Most commonly made from high-grade stainless steel, carbon steel, or other robust materials suitable for withstanding high-pressure environments, these plugs ensure that any well, pipeline, or other pressure-containing apparatus maintains its intended flow stoppage. Their design, which typically involves threaded ends, facilitates easy installation and removal, enhancing operational efficiency.
Expertise in selecting the right bull plug revolves around understanding the specifications of the environment where it will be used. Factors such as temperature, pressure ratings, and the chemical composition of transported fluids play an essential role in this decision-making process. More specifically, corrosion resistance is a prime consideration, as these plugs often face harsh chemical environments that can lead to premature degradation.
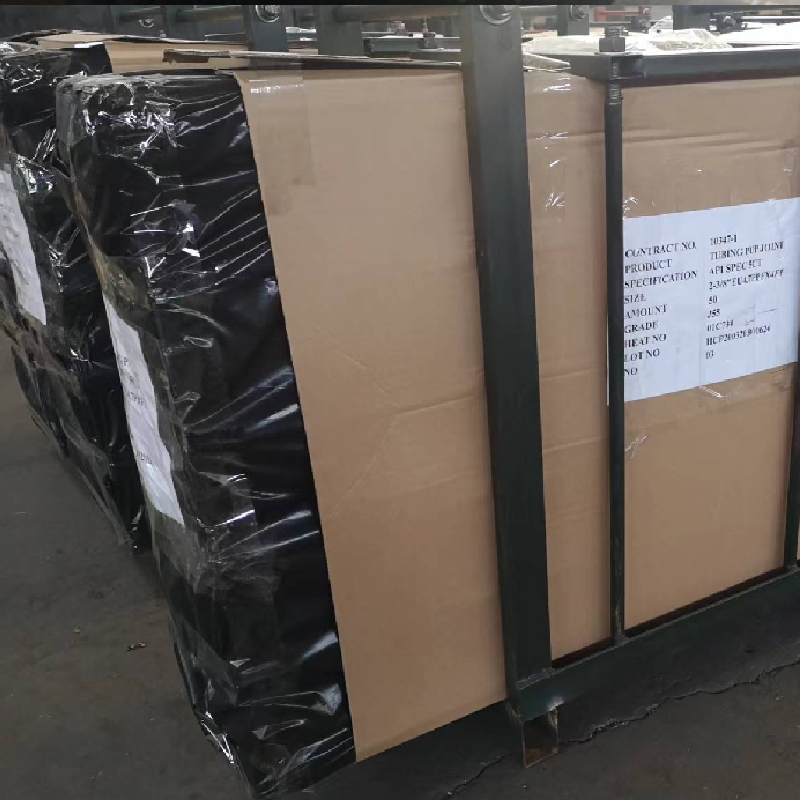
From an operational standpoint,
professionals emphasize the bull plug's role in safety. In scenarios where a section of the pipeline needs to be isolated for maintenance or emergency reasons, a properly rated bull plug can prevent accidents caused by uncontrolled fluid escape. The plug acts as a physical barrier, creating a temporary halt in the flow, allowing engineers to conduct necessary inspections or repairs without compromising worker safety or environmental health.
what is bull plug
Through the lens of authoritative knowledge, it's important to recognize the bull plug's role in regulatory compliance. Industry standards and certifications, such as those from the American Petroleum Institute (API), dictate the specifications that bull plugs must meet to ensure they perform reliably under stated conditions. Adhering to these standards is crucial for any oil and gas operation, not only to promote safety but to avoid the legal repercussions of non-compliance.
Trustworthiness in a bull plug's performance is often demonstrated through field testing and historical case studies. Longitudinal data gathered from various drilling sites globally offer insights into their effectiveness over years of use, highlighting not only their durability but also the situations that can lead to failures. Such data underscores the importance of selecting a bull plug from reputable manufacturers who provide solid warranties and comprehensive customer support.
For product-focused domains, the experience with bull plugs must include a conversation about technological advancements. Smart technologies and IoT integration have begun to feature in modern bull plug design, offering real-time status monitoring and predictive maintenance alerts. Such innovations further enhance the tool's effectiveness, reducing downtime and ensuring smooth, uninterrupted operations in oil fields worldwide.
In conclusion, the bull plug serves an indispensable role in the oil and gas industry, marrying experience, expertise, authority, and trust in its deployment. With ongoing advancements and strict adherence to international standards, these dynamic components continue to underpin the successful and safe management of fluid systems across the globe. For industry professionals, understanding the nuances of bull plug selection and application is not merely a technical requirement but a pivotal factor in operational success and safety.