In the world of oil and gas extraction, the understanding of downhole equipment is vital for efficiency, safety, and cost-effectiveness.
Two fundamental components of this process are casing and tubing. Though these terms are sometimes used interchangeably by those outside the industry, they play distinct roles in drilling operations.
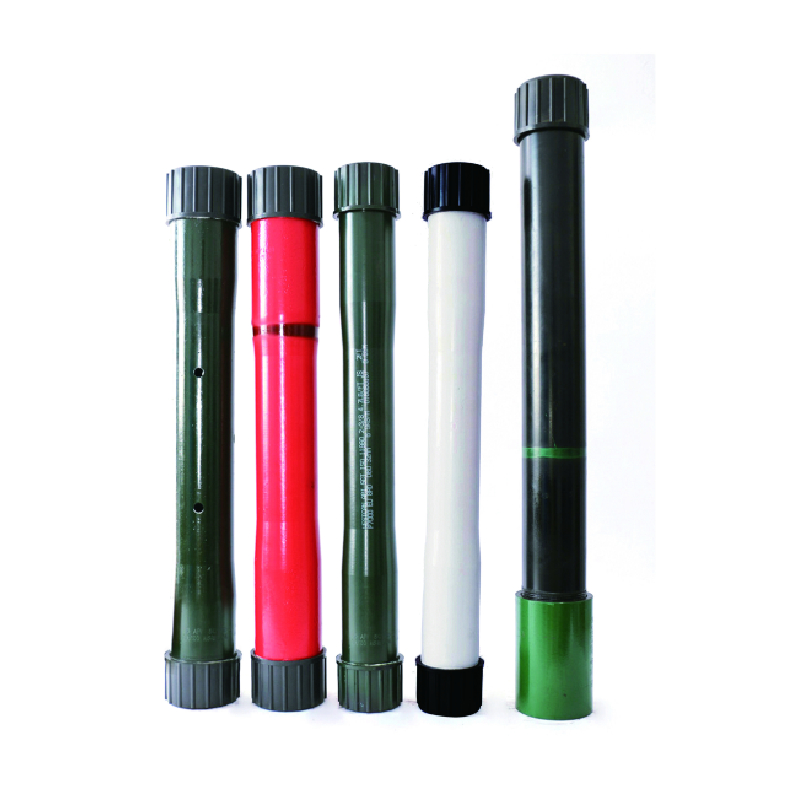
Casing and tubing are both crucial to creating productive oil wells, yet their functions, materials, and deployment processes differ significantly. This article delves into the disparities between these two critical elements, fortified by expert insights and experiential understanding.
Casing The Protective Barrier
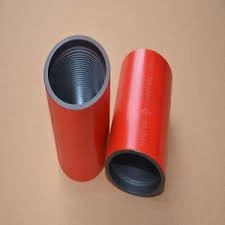
Casing serves as the backbone of the well structure. Once a well is drilled, steel pipes known as casing are installed to stabilize the sides of the well. These casings are cemented in place to protect groundwater from contamination and maintain borehole integrity.
From an expert perspective, one must recognize that casing can consist of multiple layers, each serving a specific purpose according to the drilling stage. Surface casing begins the process, guarding freshwater zones, while subsequent intermediate and production casings advance drilling depth while facing increasing pressure and temperature demands.
Casing sizes can vary significantly, often ranging from 4.5 to 20 inches in diameter. The choice of casing size is impacted by well configuration and geological considerations. In challenging oil fields, expert selection of casing material, such as high-strength steel or corrosion-resistant alloys, can mean the difference between success and operational failure.
Tubing The Production Pathway
Conversely, tubing acts as the conduit for oil and gas extraction. Installed within the casing, tubing enables hydrocarbons to flow to the surface. Unlike casing, tubing is not permanently cemented, allowing for removal and replacement as needed, which is an operation-savvy approach recognized by industry professionals.
A pivotal attribute of tubing is its adaptability to varying pressure and thermal conditions encountered during production. Tubing diameters are generally smaller than casing, ranging from 1.05 to 4.5 inches, allowing for versatile deployment in both low-flow and high-pressure environments.
For enhanced credibility in production processes, tubing often incorporates advanced materials such as chromium, stainless steels, or specialized polymers. These materials resist corrosion and wear, ensuring the longevity and reliability of operations. The strategic selection of tubing materials and configurations is underpinned by expertise in fluid dynamics and an understanding of the produced hydrocarbon types.
what is the difference between casing and tubing?
Key Differences Concrete Insights
Understanding the distinctions between casing and tubing can be solidified through these expert-created insights
1. Functional Purpose Casing provides structural stability, whereas tubing is designed for fluid transport.
2. Installation Method Casing is cemented in place permanently, while tubing is retrievable, offering operational flexibility.
3. Material Specifications The composition of casing focuses on structural integrity, while tubing materials prioritize flow dynamics and corrosion resistance.
4. Dimensional Considerations Larger diameters suit casing requirements for space within wellbores, while smaller tubing sizes accommodate efficient hydrocarbon flow.
5. Lifecycle and Maintenance Casing must endure the well's life, needing meticulous initial selection and placement; tubing can be maintained, replaced, or upgraded as production demands evolve.
Trust and Reliability Anchored in Expertise
When drilling for oil and gas, choosing the correct casing and tubing can elevate operational success and mitigate unforeseen risks. With experience comes the wisdom to tailor selections according to the nuanced requirements of specific drilling environments. Engineers and geologists collaborate, blending their insights with empirical data to achieve optimal outcomes.
The authoritativeness of choosing the precise casing and tubing is not just theoretical—real-world applications demonstrate tangible benefits in safety, efficiency, and cost management. Through consistent selection refinement and using established industry guidelines, operational teams reinforce trust in drilling systems and their enduring effectiveness.
In conclusion, effective differentiation and application of casing and tubing are cornerstones of successful oil and gas extraction. Their distinct roles underpin all well-designed drilling operations, ensuring both the integrity of the wellbore and the efficiency of production flows. Embracing expert advice and up-to-date industry practices fosters not only effective resource extraction but also steadfast operational safety and reliability.