In the oil and gas industry, casing and tubing are critical components whose roles and applications are often misunderstood. While they may appear similar in function to those unfamiliar with the petroleum sector, they serve distinctly different purposes in the wellbore architecture. Understanding the nuanced differences between casing and tubing is essential for anyone looking to engage in or comprehend oilfield activities, contributing to an informed discussion on production optimization and cost-efficiency.
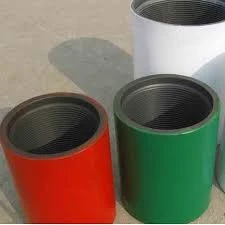
Casing is a large diameter pipe, cemented in place, that forms the foundational structure of a wellbore. Its primary role is to maintain the integrity of the well, prevent contamination of water sands, support unstable upper formations, isolate different pressure zones, and to prevent hydrocarbons from being released uncontrollably. The deployment of casing begins after the well has been drilled to a predetermined depth. Numerous types of casings—conductor, surface, intermediate, production, and liner—are used sequentially to ensure structural stability throughout the well drilling and completion phases.
The conductor casing is installed first to prevent the loose surface sediment from caving into the wellbore. Surface casing follows, sealing off freshwater formations and serving as a critical blowout prevention element. Intermediate casing, utilized in deeper locations, provides the structural strength necessary to traverse over-pressurized zones. Finally, production casing is set across the reservoir zone, providing a conduit path for the eventual extraction of oil and gas.
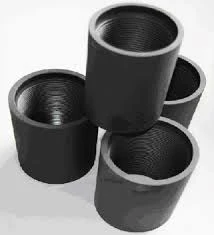
Tubing, in contrast, is a narrower pipe placed within the casing string during the completion phase of a well. Its central function is to provide an efficient path for oil and gas to flow from the reservoir to the surface. This narrower diameter maximizes the energy efficiency of the extraction process by reducing friction and flow resistance.
A distinctive characteristic of tubing is its provision for easy removal and replacement, allowing for routine maintenance and control of production rates. Tubing can be tailored with various configurations such as tubing anchors, packers, and other completion tools that optimize its operation in varied reservoir conditions.
what is the difference between casing and tubing?
Aside from their functional differences, casing and tubing differ in specifications and materials tailored to their purposes. Casing is generally constructed from high-strength steel to withstand external pressures, prevent collapse, and protect the well from corrosive or erosive elements. Materials are selected based on specific well conditions, including the chemical properties of the gas or oil, the temperature, and the pressure environment.
Meanwhile, tubing, made from a variety of steels or even corrosion-resistant alloys, is designed to withstand internal pressures and corrosive fluids. These materials ensure the longevity and efficiency of the tubing, reflecting its direct contact with flowing hydrocarbons. This choice of material is critical as the tubing must maintain its integrity over time while facilitating uninterrupted production flow.
Performance monitoring of these components is crucial. Casing integrity needs to be assessed by logs and pressure tests to detect leaks or signs of failure before they compromise well operations. Tubing, being more frequently handled, is subject to periodic inspections to detect wear, corrosion, or blockage that might hinder optimal production.
In conclusion,
understanding the role and differences between casing and tubing is crucial for optimal well design and operation. Their roles are complementary yet distinct casing provides the indispensable structural and pressure boundaries for a well, while tubing ensures effective transportation of hydrocarbons from the reservoir to the surface. This nuanced comprehension contributes to industry best practices, operational safety, and overall economic feasibility. Advanced materials and technological approaches continually enhance the performance and reliability of both casing and tubing in the ever-challenging environments of oil and gas extraction.